Why Absolute Pressure Transducer is More Prone to Zero Drift
It is well known that pressure transducers can be classified into absolute pressure transducers, gauge pressure transducers and differential pressure transducers depending on the type of measured pressure. In this paper, the absolute pressure transducer is compared with the gauge pressure and differential pressure transducer. The reasons for the zero drift of the absolute pressure transducer are analyzed from the aspects of principle, practical application and operation.
1. Measuring principle and structural reasons of absolute pressure transducer
When the pressure transducer measuring the pressure, the medium pressure is transmitted to the measuring diaphragm through the isolation diaphragm at high and low sides and filling oil. The measuring diaphragm at the center of the measuring chamber. Using the direct digital circuit, the position of the measuring diaphragm is detected through the fixed plate on both sides. As shown in following figure.
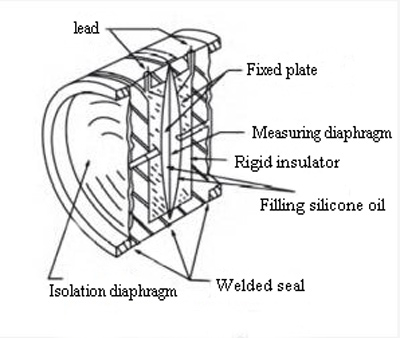
For gauge and differential pressure transducers, if the atmospheric pressure is applied to the low pressure side and the sensing diaphragm at the same time, the diaphragm has a symmetrical structure at the high pressure side without pressure. It makes it easy to achieve pressure balance. However, for the absolute pressure transducer, the low pressure side always maintains a reference pressure (that is, it is enclosed in a high vacuum reference chamber). Thus, the sensor diaphragm has an asymmetric structure at both ends. That is to say, regardless of the reference cavity leakage or material deformation and other factors will lead to zero point change, that is, zero drift of absolute pressure transducer.
2. The inference of the on-site environment on absolute pressure transducers
The stability of the absolute pressure transducer is greatly affected by temperature. Take the application of the absolute pressure transducer in the nuclear plant as an example. For pressure transducers installed in cooling water pipes, the temperature of the contact medium is often as high as 100 ℃. When these absolute pressure transducers are operating under high temperature and vacuum conditions, the isolation diaphragm in the cavity is drummed due to the vacuum. Then the pressure in the sealing system reduces and the viscosity of the filling liquid also reduces. It leads to volatile enhancement for silicone oil, lower boiling point and enhanced thermal expansion. Part of the silicone oil appears to be vaporized and volume-expanded, which deforms the isolating diaphragm and causes zero drift.
3. Calibration for absolute pressure transducer is incorrect
When the user periodically calibrating the absolute pressure transducer, the indication value is often out of tolerance. The reason is that the user often makes adjustment errors when checking the absolute pressure transducer. For example, take an absolute pressure transducer with range of 0-10 MPa and output signal of 4-20 mA as an example. In the vacuum state (ie, the very large vacuum degree that the metering device can achieve), its actual output current value (referred to as the actual output value) is smaller than the theoretical output value. The analysis found that the theoretical output of the 0-10 MPa range absolute pressure transducer at atmospheric pressure (standard atmospheric pressure is 101.321 kPa) is 4.162 mA, which is close to 4 mA. At this time, many users will mistakenly treat these absolute pressure transducers as gauge pressure transducers. It is directly cleared in the atmospheric pressure environment. It causes the actual output of the absolute pressure transducer to be lower than the theoretical output value under vacuum status.
Some users often make incorrect adjustments to the full scale of the absolute pressure transducer relative to the misalignment for the zero adjustment. Take an absolute pressure transducer with range of 0-100 kPa and output signal of 4-20 mA as an example. Its theoretical output at 100 kPa absolute should be 20 mA. If the local atmospheric pressure is 102 kPa, the theoretical output current should be 20.32 mA. When the user finds that the output current of these absolute pressure transducers is higher than 20 mA, the pressure transducer will be erroneously adjusted to full-scale current at atmospheric pressure. It causes the range of the absolute pressure transducer to expand and it also affects its zero current.
- Overview of the zero drift in the absolute pressure transducer
- Reasons for the zero drift of absolute pressure transducer
1. Measuring principle and structural reasons of absolute pressure transducer
When the pressure transducer measuring the pressure, the medium pressure is transmitted to the measuring diaphragm through the isolation diaphragm at high and low sides and filling oil. The measuring diaphragm at the center of the measuring chamber. Using the direct digital circuit, the position of the measuring diaphragm is detected through the fixed plate on both sides. As shown in following figure.
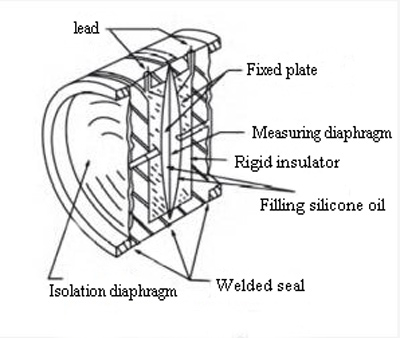
For gauge and differential pressure transducers, if the atmospheric pressure is applied to the low pressure side and the sensing diaphragm at the same time, the diaphragm has a symmetrical structure at the high pressure side without pressure. It makes it easy to achieve pressure balance. However, for the absolute pressure transducer, the low pressure side always maintains a reference pressure (that is, it is enclosed in a high vacuum reference chamber). Thus, the sensor diaphragm has an asymmetric structure at both ends. That is to say, regardless of the reference cavity leakage or material deformation and other factors will lead to zero point change, that is, zero drift of absolute pressure transducer.
2. The inference of the on-site environment on absolute pressure transducers
The stability of the absolute pressure transducer is greatly affected by temperature. Take the application of the absolute pressure transducer in the nuclear plant as an example. For pressure transducers installed in cooling water pipes, the temperature of the contact medium is often as high as 100 ℃. When these absolute pressure transducers are operating under high temperature and vacuum conditions, the isolation diaphragm in the cavity is drummed due to the vacuum. Then the pressure in the sealing system reduces and the viscosity of the filling liquid also reduces. It leads to volatile enhancement for silicone oil, lower boiling point and enhanced thermal expansion. Part of the silicone oil appears to be vaporized and volume-expanded, which deforms the isolating diaphragm and causes zero drift.
3. Calibration for absolute pressure transducer is incorrect
When the user periodically calibrating the absolute pressure transducer, the indication value is often out of tolerance. The reason is that the user often makes adjustment errors when checking the absolute pressure transducer. For example, take an absolute pressure transducer with range of 0-10 MPa and output signal of 4-20 mA as an example. In the vacuum state (ie, the very large vacuum degree that the metering device can achieve), its actual output current value (referred to as the actual output value) is smaller than the theoretical output value. The analysis found that the theoretical output of the 0-10 MPa range absolute pressure transducer at atmospheric pressure (standard atmospheric pressure is 101.321 kPa) is 4.162 mA, which is close to 4 mA. At this time, many users will mistakenly treat these absolute pressure transducers as gauge pressure transducers. It is directly cleared in the atmospheric pressure environment. It causes the actual output of the absolute pressure transducer to be lower than the theoretical output value under vacuum status.
Some users often make incorrect adjustments to the full scale of the absolute pressure transducer relative to the misalignment for the zero adjustment. Take an absolute pressure transducer with range of 0-100 kPa and output signal of 4-20 mA as an example. Its theoretical output at 100 kPa absolute should be 20 mA. If the local atmospheric pressure is 102 kPa, the theoretical output current should be 20.32 mA. When the user finds that the output current of these absolute pressure transducers is higher than 20 mA, the pressure transducer will be erroneously adjusted to full-scale current at atmospheric pressure. It causes the range of the absolute pressure transducer to expand and it also affects its zero current.