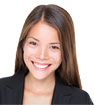
Pressure Sensor
Home » Wiki
Monocrystalline silicon pressure transducers are one of the most common pressure transducers in industrial production. Monocrystalline silicon is a good semiconducting material. The monocrystalline silicon pressure transducer is fabricated using a high performance piezoresistive pressure core.
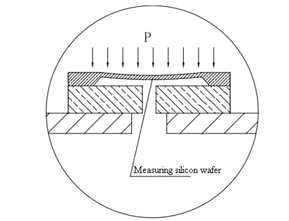
This paper describes the working principle of monocrystalline silicon pressure transducer and the realization process of high stability and high accuracy performance. The key points include the selection of monocrystalline silicon chips, the stress-free packaging of monocrystalline silicon wafers, the elimination of backlash errors, the reduction of static pressure effects, and the amplification of the range ratio. In these ways, enhance the full performance, accuracy level and reliability of the pressure transducer. As a precision measurement instrument, monocrystalline silicon pressure transducer is very common in the field of automation, which is of great significance.
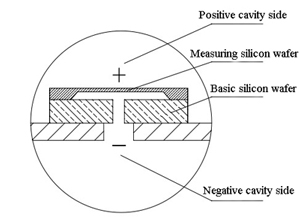
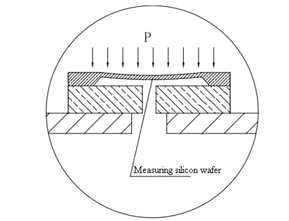
This paper describes the working principle of monocrystalline silicon pressure transducer and the realization process of high stability and high accuracy performance. The key points include the selection of monocrystalline silicon chips, the stress-free packaging of monocrystalline silicon wafers, the elimination of backlash errors, the reduction of static pressure effects, and the amplification of the range ratio. In these ways, enhance the full performance, accuracy level and reliability of the pressure transducer. As a precision measurement instrument, monocrystalline silicon pressure transducer is very common in the field of automation, which is of great significance.
A pressure sensor is a device or equipment that senses a pressure signal and converts the pressure signal into a usable output electrical signal according to a certain law. The pressure sensor are usually composed of pressure sensitive components and signal processing units. According to different measured pressure types, the pressure sensor are generally divided into absolute pressure sensors, differential pressure sensors and gauge pressure sensors.


A differential pressure sensor is also called differential pressure transducer. It is a
sensor used to measure the difference between two pressures. It is usually used to measure the differential pressure between the front and rear ends of a device or component as well as the differential pressure between different medium in the same process. Its outer casing is made of stainless steel or aluminum alloy. The connecting thread on the pressure tap is NPT1/2. The thread of the output cable connection hole is M20*1.5. Differential pressure sensors are widely used in the production process control such as electric power, coal, spinning cotton boxes, dust removal equipment and other industries.
The pressure of the measuring medium directly acts on the diaphragm of the sensor to cause the diaphragm to generate a micro-displacement proportional to the medium pressure, so that the resistance value of the sensor changes. Then the change detected by the electronic circuit, at the same time, it converts and outputs a standard measurement signal corresponding to this pressure.
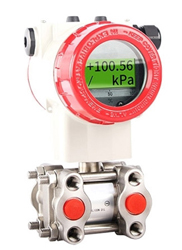
The pressure of the measuring medium directly acts on the diaphragm of the sensor to cause the diaphragm to generate a micro-displacement proportional to the medium pressure, so that the resistance value of the sensor changes. Then the change detected by the electronic circuit, at the same time, it converts and outputs a standard measurement signal corresponding to this pressure.
For the application of differential pressure sensors, zero migration processing is generally not required if the measurement conditions are enough. However, the differential pressure sensor often takes into consideration for the maintenance and installation during the actual use. In order to facilitate the operation, there is often a horizontal difference between the pressure tapping point and the measuring instrument, or when there are some limiting factors in the measured medium, such as strong corrosiveness, excessive viscosity, etc., this will cause certain obstacles to the whole pressure measurement process, and even affect the measurement accuracy of the meter. Therefore, in order to achieve accurate measurement for the differential pressure sensor as much as possible, the differential pressure sensor zero-point migration technique is usually processed. This paper will conduct a detailed analysis and research on the zero-point migration for differential pressure sensors.
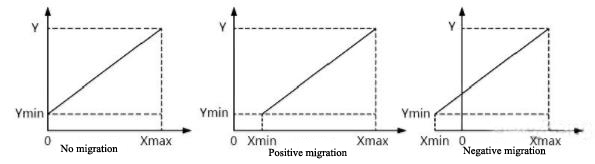
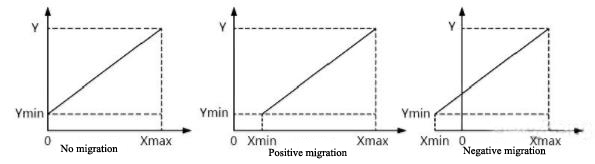
In industrial applications, 2 wire pressure transducers are definitely the first choice. In industrial production, the measuring points are generally on site, and the display device or control device is generally in the control room or control cabinet. The distance between the two will be tens of meters or even hundreds of meters. Eliminating two wires means that the cost can be reduced a lot.
The air pressure sensor is a conversion device mainly used for measuring the absolute pressure, gauge pressure and differential pressure of the gas. It is applied to pneumatic control systems and hydraulic systems for pressure measurement of wind pressure and pipeline gas, etc.
The 2-wire, 3-wire, and 4-wire of the pressure transducer refer to the wiring of the transducer. This title appeared only after the birth of the two-wire pressure transducer. It is the result of the widespread use of electronic amplifiers in the measurement of pressure sensors. The essence of amplification is an energy conversion process, which is inseparable from the power supply. Therefore, the first to appear is the four-wire pressure transducer. In this system, two wires are responsible for the supply of power, and the other two wires are responsible for outputting converted and amplified signals (such as voltage, current, etc.). The appearance of the electric unit combination meter made the four-wire pressure transducer has been widely used. The transducer’s power supply is 220VAC, and the output signal is 0-20mA DC.
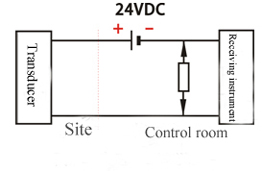
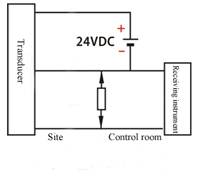

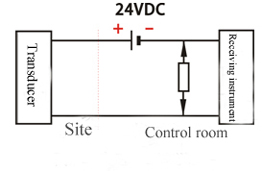
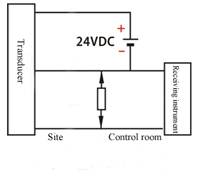

The digital pressure sensor is one kind of the pressure sensor, which has a wide
range of applications in industrial, civil, military and other industries. The reason why digital pressure sensors have important applications is mainly that it can directly display the values we need for easy observation and recording. Moreover, the digital pressure sensor can also simulate the output, which greatly meets the needs of customers. However, like any other product, the digital pressure sensor has the following disadvantages in addition to its advantages. 1. Digital pressure sensors are generally a little more expensive than sensors with normal analog outputs. 2. Digital pressure sensors are more susceptible to damage than ordinary sensors because digital sensors are output with a liquid crystal display, which is relatively easy to break. Therefore, when we use digital pressure sensors, we need to be very careful to avoid damage. Of course, as technology continues to update, the shortcomings of digital pressure sensors will gradually be compensated.
Digital pressure sensors must be selected based on the measurement range. General pressure sensors have a certain adjustable measurement range. Set using range to 14 to 34 segments of the sensor range, so the accuracy is guaranteed. In practice, some applications need to migrate the measurement range of the sensor. Calculate the measurement range and migration amount based on the site installation location. Migration has the distinction of positive migration and negative migration.
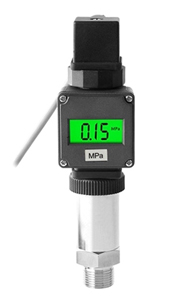
Digital pressure sensors must be selected based on the measurement range. General pressure sensors have a certain adjustable measurement range. Set using range to 14 to 34 segments of the sensor range, so the accuracy is guaranteed. In practice, some applications need to migrate the measurement range of the sensor. Calculate the measurement range and migration amount based on the site installation location. Migration has the distinction of positive migration and negative migration.
During the selection and use of the pressure transducer, three specifications of sensitivity, resolution, and error are often mentioned. However, many people are not very clear about the actual meaning and difference of these three specifications, resulting in large or small problems when using pressure transducers. This paper will explain the meaning and difference of the sensitivity, accuracy and error of the pressure transducer.
Piezoresistive pressure sensors are pressure sensors made by using the piezoresistive effect of monocrystalline silicon materials and integrated circuit technology. The sensor use monocrystalline silicon wafer as the elastic component. Using an integrated circuit process on monocrystalline silicon wafer, a set of equivalent resistance is diffused in a specific direction of monocrystalline silicon. The resistor are connected into a bridge and the monocrystalline silicon wafer is placed in the sensor cavity. When the pressure changes, the monocrystalline silicon strains, so that the strain resistance directly diffused on it generates a change proportional to the measured pressure, and the bridge circuit obtains the corresponding voltage output signal.
The digital pressure gauge is a meter for measuring and indicating the pressure of the measured medium. Its elastic components are sensitive components. Pressure gauge is a common measuring instrument and widely used in various fields. It visually displays pressure changes at various production stages and provides the necessary data reference for the process. In addition, the pressure gauge can also monitor the safety trend during production and operation, and plays an important role in preventing accidents and protecting personal and property safety. Digital pressure gauges can meet the requirements of high accuracy and low power consumption in process production. Its display uses liquid crystal display technology and the unique backlight to make the measured pressure data clear and easy to read at night. Digital pressure gauges use high-performance chips that automatically record peak pressure values and trace historical peak data. The housing is made of stainless steel and is fully resistant to corrosion and vibration. It can be used in a variety of complex environments.
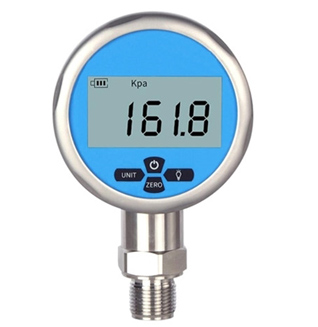
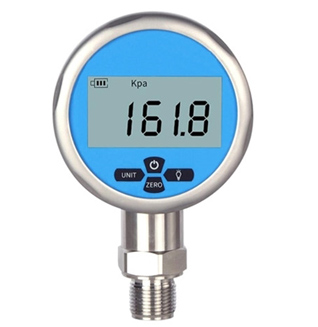
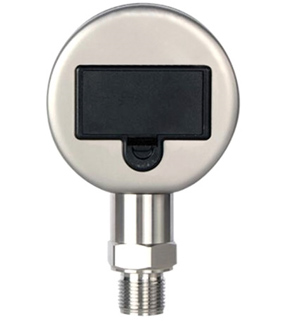