What is a Piezoresistive Pressure Sensor
Piezoresistive pressure sensors are pressure sensors made by using the piezoresistive effect of monocrystalline silicon materials and integrated circuit technology. The sensor use monocrystalline silicon wafer as the elastic component. Using an integrated circuit process on monocrystalline silicon wafer, a set of equivalent resistance is diffused in a specific direction of monocrystalline silicon. The resistor are connected into a bridge and the monocrystalline silicon wafer is placed in the sensor cavity. When the pressure changes, the monocrystalline silicon strains, so that the strain resistance directly diffused on it generates a change proportional to the measured pressure, and the bridge circuit obtains the corresponding voltage output signal.
The monocrystalline silicon material changes its resistivity under a pressure. An output electrical signal proportional to the pressure change is obtained by measuring the circuit. Piezoresistive pressure sensors are used for the measurement and control in pressure, tension, pressure difference, and other physical quantities (such as liquid level, acceleration, weight, strain, flow, vacuum) that can be converted into changes in force.
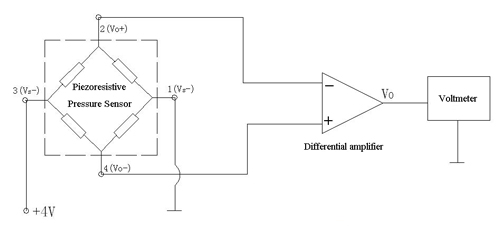
When a force acts on a silicon crystal, the crystal lattice of the crystal is deformed, causing carriers to scatter from one energy valley to another, causing a change in carrier mobility. This change disturbs the average amount of carriers in the longitudinal and lateral directions, thereby changing the resistivity of silicon.
This change varies with the orientation of the crystal, so the silicon piezoresistive effect is related to the crystal orientation. The silicon piezoresistive effect is different from metal strain gauges. The resistance change of the former with the pressure mainly depends on the change of the resistivity; the resistance change of the latter mainly depends on the change of the geometrical size, and the sensitivity of the former is 50 to 100 times larger than that of the latter.
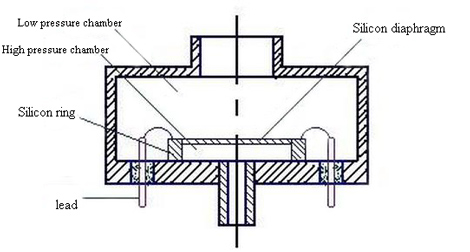
One side of the silicon diaphragm is a high pressure chamber in communication with the measured pressure, and the other side is a low pressure chamber in communication with the atmosphere. The silicon diaphragm is generally designed to a circular shape with a peripheral support, and the ratio of diameter to thickness is about 20 to 60. Disperse four P impurity resistor strips on a circular silicon diaphragm and connect them to a full bridge. Two of them are in the compressive stress zone and the other two are in the tensile stress zone, which is symmetrical with respect to the center of the diaphragm.
In addition, there are piezoresistive pressure sensors using square silicon diaphragms and silicon columnar sensitive elements. The silicon columnar sensitive element also diffuses the resistance strip in a certain direction on a certain crystal plane of the silicon cylinder surface. The two tensile stress strips and the other two stressed stress strips form a full bridge.
Due to the small size of the piezoresistive sensor, it can be constructed in a variety of packaging options. The package options are designed to eliminate the effects of mounting on bias and sensitivity, as well as low frequency output due to thermal expansion after proper installation.
2. Smaller scale, which can do more work
The final form factor of the pressure sensor is one of the more important device property for many users. Piezoresistive sensor technology offers greater flexibility than other technologies because the size of the sensing element is very small. Automotive applications include the engine's air, oil, cooling and fuel systems, braking systems, and transmissions. Typical aerospace applications are scale models and full-scale flight tests. For example, a scale model wind tunnel test object needs to measure the pressure at the leading edge portion of the fuselage, whose radius can be less than one tenth of an inch. In other applications, pressure measurements must be made in areas where the thickness of the test article is very thin and impenetrable. Only piezoresistive pressure sensors can be fabricated in sufficiently small sizes to support any of these devices.
3. Operability and robustness in extreme environments
Commercial applications in most demanding environments always use piezoresistive pressure sensors because of their small size, small weight, and robust construction. Piezoresistive pressure sensors do not require external amplifiers and special cables for technologies. Piezoresistive pressure sensors are well suited for pressure measurement in aircraft engines, nuclear, downhole, cryogenic, space, automotive motion and other extreme environments.
4. Good temperature compensation
Piezoresistive pressure sensors can be adjusted using embedded digital programming electronics. Piezoresistive pressure sensors can be linearized to ± 0.1% within full scale at constant temperature. Because the temperature predicted by bridge resistance changes and the temperature of the piezoresistive pressure sensor are extremely repeatable, embedded electronics can also be used to correct for bias and sensitivity offsets due to temperature. The temperature sensitivity of a piezoresistive pressure sensor can be controlled within ±0.001% of Fahrenheit after the sensor's electronic characteristics are programmed into the embedded regulation electronics.
5. Cost competitiveness
The installation cost of a piezoresistive pressure sensor measurement system is generally lower than that of a piezoelectric pressure sensor system. The cost of the transducer, cable, and electronics of the piezoresistive pressure sensor is less than the cost of the corresponding pressure sensor system component. Fewer individual components are also a feature of piezoresistive pressure sensor installation.
- The Piezoresistive pressure sensor working principle
The monocrystalline silicon material changes its resistivity under a pressure. An output electrical signal proportional to the pressure change is obtained by measuring the circuit. Piezoresistive pressure sensors are used for the measurement and control in pressure, tension, pressure difference, and other physical quantities (such as liquid level, acceleration, weight, strain, flow, vacuum) that can be converted into changes in force.
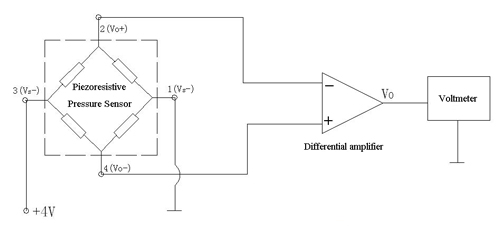
When a force acts on a silicon crystal, the crystal lattice of the crystal is deformed, causing carriers to scatter from one energy valley to another, causing a change in carrier mobility. This change disturbs the average amount of carriers in the longitudinal and lateral directions, thereby changing the resistivity of silicon.
This change varies with the orientation of the crystal, so the silicon piezoresistive effect is related to the crystal orientation. The silicon piezoresistive effect is different from metal strain gauges. The resistance change of the former with the pressure mainly depends on the change of the resistivity; the resistance change of the latter mainly depends on the change of the geometrical size, and the sensitivity of the former is 50 to 100 times larger than that of the latter.
- The Piezoresistive pressure sensor construction
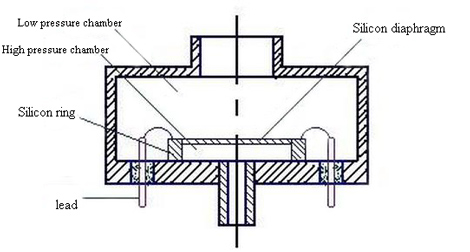
One side of the silicon diaphragm is a high pressure chamber in communication with the measured pressure, and the other side is a low pressure chamber in communication with the atmosphere. The silicon diaphragm is generally designed to a circular shape with a peripheral support, and the ratio of diameter to thickness is about 20 to 60. Disperse four P impurity resistor strips on a circular silicon diaphragm and connect them to a full bridge. Two of them are in the compressive stress zone and the other two are in the tensile stress zone, which is symmetrical with respect to the center of the diaphragm.
In addition, there are piezoresistive pressure sensors using square silicon diaphragms and silicon columnar sensitive elements. The silicon columnar sensitive element also diffuses the resistance strip in a certain direction on a certain crystal plane of the silicon cylinder surface. The two tensile stress strips and the other two stressed stress strips form a full bridge.
- Advantage Of the piezoresistive pressure sensor
Due to the small size of the piezoresistive sensor, it can be constructed in a variety of packaging options. The package options are designed to eliminate the effects of mounting on bias and sensitivity, as well as low frequency output due to thermal expansion after proper installation.
2. Smaller scale, which can do more work
The final form factor of the pressure sensor is one of the more important device property for many users. Piezoresistive sensor technology offers greater flexibility than other technologies because the size of the sensing element is very small. Automotive applications include the engine's air, oil, cooling and fuel systems, braking systems, and transmissions. Typical aerospace applications are scale models and full-scale flight tests. For example, a scale model wind tunnel test object needs to measure the pressure at the leading edge portion of the fuselage, whose radius can be less than one tenth of an inch. In other applications, pressure measurements must be made in areas where the thickness of the test article is very thin and impenetrable. Only piezoresistive pressure sensors can be fabricated in sufficiently small sizes to support any of these devices.
3. Operability and robustness in extreme environments
Commercial applications in most demanding environments always use piezoresistive pressure sensors because of their small size, small weight, and robust construction. Piezoresistive pressure sensors do not require external amplifiers and special cables for technologies. Piezoresistive pressure sensors are well suited for pressure measurement in aircraft engines, nuclear, downhole, cryogenic, space, automotive motion and other extreme environments.
4. Good temperature compensation
Piezoresistive pressure sensors can be adjusted using embedded digital programming electronics. Piezoresistive pressure sensors can be linearized to ± 0.1% within full scale at constant temperature. Because the temperature predicted by bridge resistance changes and the temperature of the piezoresistive pressure sensor are extremely repeatable, embedded electronics can also be used to correct for bias and sensitivity offsets due to temperature. The temperature sensitivity of a piezoresistive pressure sensor can be controlled within ±0.001% of Fahrenheit after the sensor's electronic characteristics are programmed into the embedded regulation electronics.
5. Cost competitiveness
The installation cost of a piezoresistive pressure sensor measurement system is generally lower than that of a piezoelectric pressure sensor system. The cost of the transducer, cable, and electronics of the piezoresistive pressure sensor is less than the cost of the corresponding pressure sensor system component. Fewer individual components are also a feature of piezoresistive pressure sensor installation.