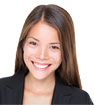
Pressure Sensor
Home » Application
The calibration for the differential pressure transducer mainly includes range adjustment and zero migration. To ensure the normal operation of the differential pressure transducer and the accuracy of differential pressure and flow measurement, users need to periodically check and calibrate it. The differential pressure transducer has a positive pressure terminal and a negative pressure terminal. In general, the pressure at the positive pressure terminal should be greater than the pressure at the negative pressure terminal so that the measurement can be performed normally. In the actual calibration process, users often mistake that the range of the differential pressure transducer can be changed by the HART communicator, and the zero point and the range adjustment can be performed without inputting the pressure source. In fact, this method only sets the range and does not meet the calibration purpose. The correct calibration should be to use the standard instrument for zero and range calibration in the case of external force, and carry out the necessary range migration according to the actual working conditions on site.
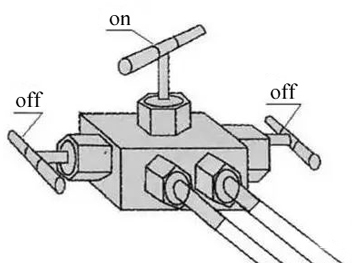
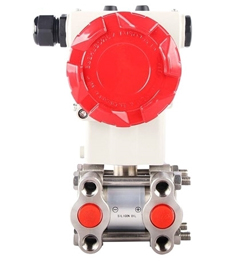
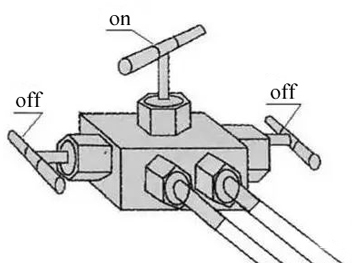
This article will introduce the method of zero adjustment for the absolute pressure transducer. Verification and calibration are performed using a pressure controller in conjunction with a mechanical pump. In the actual use of the absolute pressure transducer, due to environmental factors, human factors, etc. there will often be zero drift. Therefore, zero calibration is often required when calibrating the absolute pressure transducer.
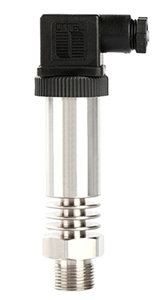
Pressure transducers are widely used in many industrial and living areas. Pressure transducers measure the pressure of various medium to maintain pressure values in a stable, safe dimension. Once the pressure value exceeds the specified dimension, the system will issue a warning to remind the user making timely adjustments to avoid accidents. High temperature pressure transducers are characterized by simple structure, ruggedness, high stability, high accuracy and good linearity. These features make it a wide measurement range. High temperature pressure transducers are widely used in various industrial automation environments.
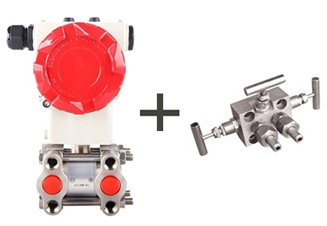
During the measurement process, there are often some failure to monocrystalline silicon differential pressure sensors for some reason. Timely analysis and processing for the failure is critical to ongoing production. Monocrystalline silicon differential pressure sensors have high stability, low temperature drift and high accuracy. However, industrial site conditions are often complex and harsh. The strong corrosiveness and strong electromagnetic interference of the application environment is a severe test for the normal operation of the differential pressure sensor. Therefore, based on practical experience, this paper summarizes the failure and the corresponding treatment methods for monocrystalline silicon differential pressure sensors.
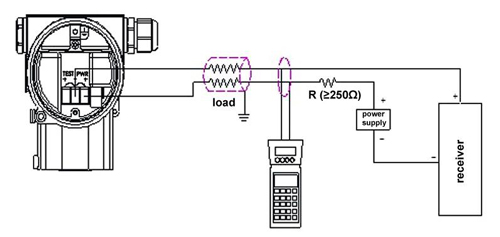
In a system that uses an indirect method to measure the mass and flow rate of steam using a mass flow meter, the steam density is generally determined based on steam pressure and temperature. Due to the different installation positions of the pressure sensor, the condensed water in the pressure tube is different. What is the impact of this situation on flow measurement and how to deal with it?
In the pressure measurement for the steam, there will be a certain difference between the pressure measured by the pressure sensor and the actual steam pressure due to the gravity of the condensed water in the pressure guiding tube.
In the pressure measurement for the steam, there will be a certain difference between the pressure measured by the pressure sensor and the actual steam pressure due to the gravity of the condensed water in the pressure guiding tube.
The connection method of the pressure sensor generally include two-wire system, three-wire system, four-wire system, and some sensors have a five-wire system.
The two-wire pressure sensor is relatively simple, and customers generally know how to wire. Connect a line is to the positive pole of the power supply, and the other line that is the signal line connected to the negative pole of the power supply through the instrument. This is the simplest. The three-wire pressure sensor add a wire to the two-wire system. This wire directly connect the negative pole of the power supply, which is more troublesome than the two-wire system. The four-wire pressure sensor has two power inputs and the other two are signal outputs. Most of the four-wire system is voltage output instead of 4-20mA output. The 4-20mA machine called pressure transmitter, and most of them are two-wire system. Some of the signal output of the pressure sensor without amplification. The full-range output is only a few tens of millivolts, and some pressure sensors have an internal amplification circuit, whose full-range output is 0-2V. As for how to connect to the display meter, it depends on how large the meter's range is.
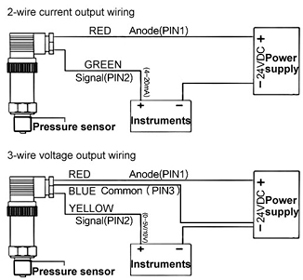
Both the pressure transducer and the differential pressure transducer need to be cleaned regularly. Dust, grease, and tiny particles in the measured medium will deposit in the pressure guiding tube or the sampling valve, directly or indirectly affecting the measurement effect. Therefore, regular cleaning is very important for the normal use of pressure transducers. Before cleaning the pressure transducer, it should be stopped and close the sampling valve. For pressure transducers that use isolation fluid, it can not be cleaned at will, but the isolation fluid should be replaced periodically.
Properly stopping and starting pressure sensors and differential pressure sensors is one of the skills that users need to master. Because during the daily use, checking the zero position for the pressure sensor and differential pressure sensor and periodically discharging the sensor will involve the starting and stopping of the sensor.
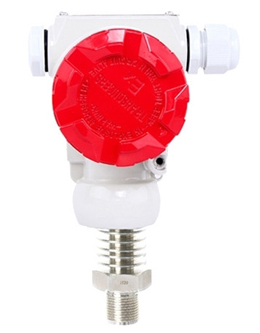
In industry, products that presented as gaseous state at normal temperature and pressure are collectively referred to as gas products, including hydrogen, oxygen, nitrogen, helium, neon, krypton, argon, helium, chlorine, carbon monoxide, and the like. Depending on the nature of the gas, the pressure measurement of each gas has different requirements. Inside the gas pressure sensor, there is an intake pipe that allowing air to enter the sensor. Once energized, the air can be connected to the inside of the pressure sensor. When the gas enters, the pressure that squeeze the sensor is generated. By capturing the amount of current inside the circuit, it is possible to transmit electronic signals simply by the magnitude of the pressure. Thereby, a working signal is sent to the device controlled by the gas pressure sensor to make it move and complete a whole set of work.
It is difficult for a differential pressure transducer to measure the level of a cryogenic liquid below -20 ℃. If we need to measure the liquid level of low temperature medium such as liquid ammonia and liquid nitrogen, we can use indirect measurement by gas isolation. As shown in the figure, the purpose for measuring the liquid level of the low temperature medium is achieved by measuring the gas pressure in the pressure guiding tube. Since the liquid in the pressure guiding tube on the high pressure side is at a normal temperature state above the boiling point, the liquid in the pressure guiding tube evaporates into a gas until a saturated gas is formed in the pressure guiding tube. When selecting a differential pressure transducer for measurement, the method uses the principle of liquid column static pressure. At this time, the pressures on the high and low pressure sides in the differential pressure transducer are as follows respectively: PH=Hx×ρ+Px ; PL=Px
Absolute pressure sensors for absolute or vacuum pressure measurement in industrial production. This paper combines the cases of absolute pressure sensors in actual use, and introduces the troubleshooting and field installation experience for absolute pressure sensors from five aspects.