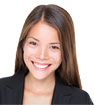
Pressure Sensor
Home » Application » Page 2
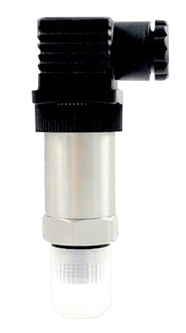
In industrial process control instruments, sensors are the most wide and common in use, which can be classified into pressure sensors and differential pressure sensors. Pressure sensors are commonly used to measure pressure, differential pressure, vacuum, liquid level, flow, and density. The pressure sensor is divided into two-wire system, three-wire system and four-wire system, two-wire sensor is more common. In addition, according to the measurement medium, it can be divided into pressure sensors, hydraulic sensors, oil pressure sensors and diaphragm pressure sensor for viscous liquid, and so on.
The pressure sensors selection is usually considered in terms of installation conditions, environmental conditions, instrument performance, economy, and measurement medium. In practical applications, there are direct measurement and indirect measurement. Its uses include process measurement, process control and device interlocking. Most used pressure sensors are normal pressure sensors and differential pressure sensors.
For 4-20mA pressure transducer, two-wire and three-wire are used more in industrial production. The 4-20mA circuit failure often occur. This article will share the troubleshooting and processing experience for the 4-20mA circuit in the two-wire pressure transducer and the 4-20mA circuit in the three-wire pressure transducer in different power supply modes.
In liquid level measurement, the pressure transducer and the liquid level sensor are two sensors that are commonly used in various types of equipment or projects. The measurement principle of these two sensors are the same. Although the two sensors are similar, there are some differences. This paper explains the difference between the pressure transducer and the liquid level sensor in liquid level measurement in principle, classification and application.
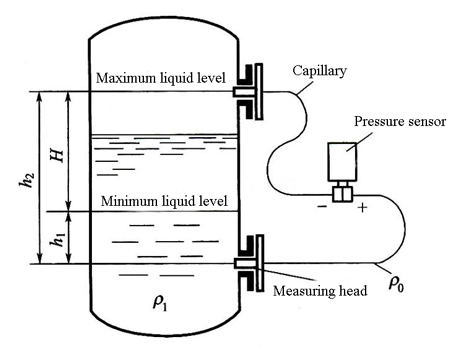
The hydraulic pressure sensor are common applications in most modern water distribution systems. In current industrial applications, pressure sensors and digital pressure gauges are the two most widely used in water distribution systems. A pressure gauge is a meter that measures and indicates fluid pressure with a resilient element as a sensitive component. Pressure gauges have existed for centuries and have proven to be accurate and reliable. Compared to the characteristics of the pressure gauge not outputting the signal, the pressure sensor converts the measured pressure into a standard current signal output.
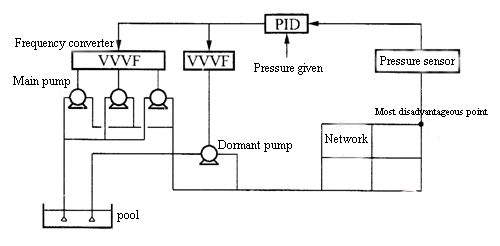
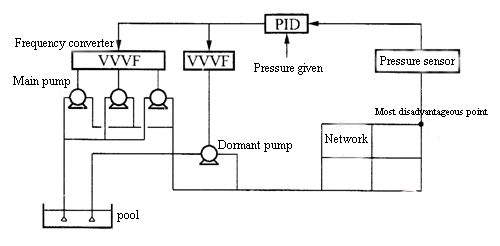
The accuracy of a pressure sensor affected by three specifications: error, precision, and uncertainty. In actual work, it is easy to confuse or misuse the three. This article will start with the definition, elaborating the connection and difference between the three.
In all various of industries, applications of the pressure sensor are more and more wide. In the petrochemical industry, especially in large-scale chemical projects, pressure sensors are one of the most used measuring devices for automatic control equipment. In water and wastewater treatment processes, pressure sensors provide an important means of control and monitoring for system protection and quality assurance.

The pressure sensor stability is a performance that make the sensor to remain unchanged after using a certain time. When selecting a pressure senor, the stability is an important specification affecting future use. This article lists four methods to help users easily judge the pressure sensor stability. These methods are simple and practical and avoid the selection of pressure sensors with poor stability.
The pressure change leak detection method is to measure the total leak rate of the tested product by using the pressure change in the sealed container inside the tested product. According to the pressure types measured by the selected pressure sensor, the pressure change method is divided into vacuum pressure change method, differential pressure change method, and absolute pressure change method.
In order to improve the measurement accuracy, pressure sensors mostly have a zero migration device, which can migrate the zero point of the sensor, that is, the starting point of the range, in the positive and negative directions. In practical applications, migration can be divided into three types: no migration, negative migration, and positive migration.
The measuring range of the sensor is equal to the sum of the range and the migration amount, that is, the measuring range = range + migration amount. As shown in the figure, the A range is 40 kPa, the migration amount is -40 kPa, and the measuring range is -40 to 0 kPa; B range is 40kPa, no migration, the measuring range is 0-40kPa; The C range is 40 kPa, the migration amount is 40 kPa, and the measuring range is 40-80 kPa.
The measuring range of the sensor is equal to the sum of the range and the migration amount, that is, the measuring range = range + migration amount. As shown in the figure, the A range is 40 kPa, the migration amount is -40 kPa, and the measuring range is -40 to 0 kPa; B range is 40kPa, no migration, the measuring range is 0-40kPa; The C range is 40 kPa, the migration amount is 40 kPa, and the measuring range is 40-80 kPa.
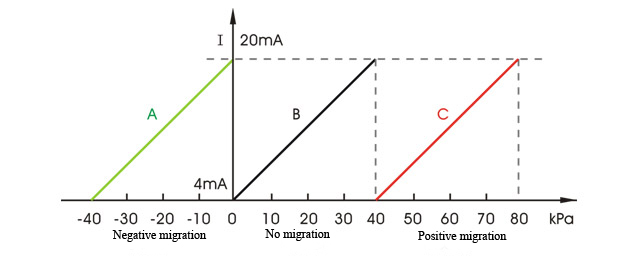
The differential pressure sensor is widely used in industrial applications. It is prone to inaccurate measurement and error during operation. What is the cause? This paper will analyze the error of the differential pressure sensor.
This article describes the online calibration method for pressure transducers used in oil gas pipelines.The pressure transducer are important monitoring and control instruments for oil pipelines. It plays a vital safety protection role in the normal operation of the entire pipeline. The pressure transducer can monitor the pressure data collected in the field and display it synchronously to the monitoring host of the station control room. It can alarm the abnormal pressure value and feed back the abnormal situation to the station staff. At the same time, the pressure transducer can also perform the switch control of the corresponding pipeline valve through the designed control program according to the collected pressure. It will help avoid serious safety incidents. Therefore, the accuracy of the pressure value measured by the pressure transducer must be guaranteed by traceability. Otherwise, it is easy to cause false alarms and misoperations, resulting in unnecessary losses.


Differential pressure level sensor has been widely used in liquid level measurement for steam condensate balance tank of the nuclear power plant. The use of liquid differential pressure sensors makes the liquid level measurement work stable, high measurement accuracy, easy to maintain and economical. However, during the installation and debugging process, various problems still occur. It requires users to have a clear understanding of the measurement principle, installation requirements, migration calculation methods of liquid differential pressure sensors. Only in this way, the measurement accuracy of the condensate balance tank level can be ensured.