Liquid Differential Pressure Sensor Used in Nuclear Power Plant
Differential pressure level sensor has been widely used in liquid level measurement for steam condensate balance tank of the nuclear power plant. The use of liquid differential pressure sensors makes the liquid level measurement work stable, high measurement accuracy, easy to maintain and economical. However, during the installation and debugging process, various problems still occur. It requires users to have a clear understanding of the measurement principle, installation requirements, migration calculation methods of liquid differential pressure sensors. Only in this way, the measurement accuracy of the condensate balance tank level can be ensured.
The level measurement system of the steam condensate balance tank uses the differential pressure level measurement principle. The system settings are shown in the flow chart of following figure. The liquid level measurement system is mainly composed of pressure vessel, balance vessel, balance vessel water supply pipeline, communication pipe, instrument root valve, differential pressure sensor ATO-PRES-2051 and pressure piping. The balance vessel is set up to avoid errors due to vapor condensation at the gas measurement end of the differential pressure sensor. In addition, it also avoids damage to the measurement instrument caused by high temperature steam. The workflow and principles are as follows.
The balance tank is installed above the measured container. The middle of the balance tank is connected to the intake line at the upper portion of the condensate tank through pipeline. Before the system is commissioned, the balance container is first hydrated by the water supply line at the top of the balance tank. When the liquid in the balance tank exceeds the connector of the communication pipe, the excess liquid automatically flows into the waste storage tank to stop the hydration. At this time, the air pressure in the upper portion of the balance tank is consistent with the air pressure in the upper portion of the waste liquid storage tank. One end of the differential pressure sensor is connected to the pressure port at the bottom of the waste liquid storage tank, and the other end is connected to the pressure port at the bottom of the balance tank. According to the differential pressure level measurement principle, the differential pressure value actually measured by the differential pressure sensor can be converted by formula, then obtain the real-time liquid level of the waste liquid storage tank.
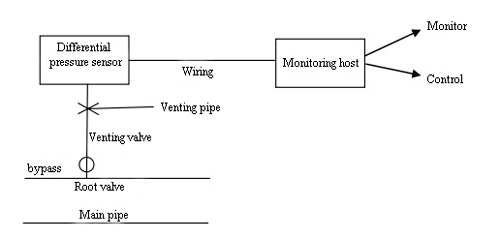
Through analysis, the reasons for this situation are as follows. Users select the instrument according to the process input conditions. The input condition is that the level of the tank needs to be measured. The measuring range is 0-500mm. The user is unclear about the installation method and measurement principle of the liquid differential pressure sensor. The user did not consider that the selection for the meter range is related to the position of the meter balance tank, but was designed according to the process input conditions. It has caused the meter not to be applicable to site. Therefore, the user should master the measurement principle and installation method of the liquid level measurement instrument before selecting the liquid differential pressure sensor.
Program 2 needs to consider the possibility of reducing the height of the balance tank. Based on the principle that the liquid in the balance tank is returned to the storage tank, the pipeline from the balance tank to the upper outlet pipe of the storage tank should be laid down slightly horizontally. Therefore, while the balance tank is falling, the connection line should also drop at the same time. After researching the equipment drawings, the distance from the pressure tap at the bottom of the tank to the top outlet of the equipment is about 550 mm. Therefore, the program is feasible. The on-site pipeline and insulation device have been installed. Changing the height of the balance tank will involve the work of the water supply pipeline, the balance tank connection pipeline, and the disassembly of the insulation layer. As a result, the workload is large. However, in order to meet the charging time node, the solution is finally adopted.
- Application of liquid differential pressure sensor in liquid level measurement system
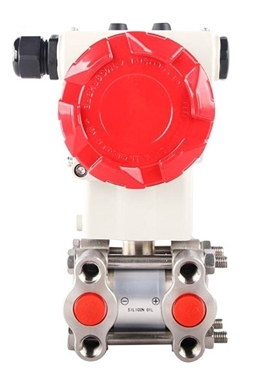
The balance tank is installed above the measured container. The middle of the balance tank is connected to the intake line at the upper portion of the condensate tank through pipeline. Before the system is commissioned, the balance container is first hydrated by the water supply line at the top of the balance tank. When the liquid in the balance tank exceeds the connector of the communication pipe, the excess liquid automatically flows into the waste storage tank to stop the hydration. At this time, the air pressure in the upper portion of the balance tank is consistent with the air pressure in the upper portion of the waste liquid storage tank. One end of the differential pressure sensor is connected to the pressure port at the bottom of the waste liquid storage tank, and the other end is connected to the pressure port at the bottom of the balance tank. According to the differential pressure level measurement principle, the differential pressure value actually measured by the differential pressure sensor can be converted by formula, then obtain the real-time liquid level of the waste liquid storage tank.
- Installation of the liquid differential pressure sensor
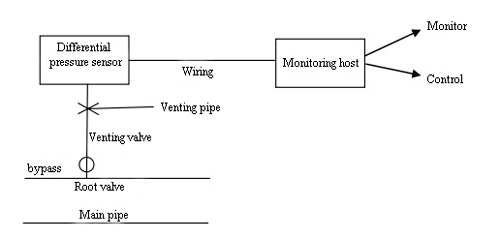
- The installation height of the liquid differential pressure sensor should be less than 0% of the container level.
- The installation height of the balance tank should be higher than the pressure tap on the upper part of the vessel. The connection line between the vessel and the balance tank should be at least 2% slope. It ensures that excess liquid that is replenished or condensed in the balance tank is returned to the vessel to maintain the pressure measured by the sensor and the balance tank be constant.
- The pressure tap on the upper part of the container should be higher than the 100% container level.
- The pressure line connecting the meter root valve to the liquid differential pressure sensor should be kept at least 2% down. It will prevent gas collection in the pressure tank.
- Liquid differential pressure sensors should be installed in areas with low radiation doses (yellow, green or white area) for on-site maintenance.
- Analysis and treatment for on-site installation and debugging of liquid differential pressure sensor
- problem analysis
Through analysis, the reasons for this situation are as follows. Users select the instrument according to the process input conditions. The input condition is that the level of the tank needs to be measured. The measuring range is 0-500mm. The user is unclear about the installation method and measurement principle of the liquid differential pressure sensor. The user did not consider that the selection for the meter range is related to the position of the meter balance tank, but was designed according to the process input conditions. It has caused the meter not to be applicable to site. Therefore, the user should master the measurement principle and installation method of the liquid level measurement instrument before selecting the liquid differential pressure sensor.
- Problem solution
- Replace the range of the liquid differential pressure sensor. Select a differential pressure sensor with the maximum range greater than 11 kPa.
- Reduce the height of the balance tank by about 500mm, so that the existing instruments can meet the requirements of on-site measurements.
Program 2 needs to consider the possibility of reducing the height of the balance tank. Based on the principle that the liquid in the balance tank is returned to the storage tank, the pipeline from the balance tank to the upper outlet pipe of the storage tank should be laid down slightly horizontally. Therefore, while the balance tank is falling, the connection line should also drop at the same time. After researching the equipment drawings, the distance from the pressure tap at the bottom of the tank to the top outlet of the equipment is about 550 mm. Therefore, the program is feasible. The on-site pipeline and insulation device have been installed. Changing the height of the balance tank will involve the work of the water supply pipeline, the balance tank connection pipeline, and the disassembly of the insulation layer. As a result, the workload is large. However, in order to meet the charging time node, the solution is finally adopted.