Selecting a Pressure Sensor According Practical Application
The pressure sensor selection must combined with the requirements of the actual application on site, because it is related to the stability of the pressure sensor and the length of its service life. This paper will introduce the classification, selection basis and application of pressure sensors in detail.
The pressure sensors selection is usually considered in terms of installation conditions, environmental conditions, instrument performance, economy, and measurement medium. In practical applications, there are direct measurement and indirect measurement. Its uses include process measurement, process control and device interlocking. Most used pressure sensors are normal pressure sensors and differential pressure sensors.
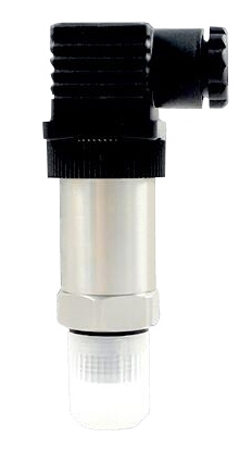
1. Structurally distinguish the pressure sensor and the differential pressure sensor, there are common type and diaphragm type. There is one measuring diaphragm in the common pressure sensor, which directly senses the pressure and differential pressure of the measured medium. The measuring diaphragm of the diaphragm pressure sensor receives the pressure of a stabilizing liquid (generally silicone oil), and the stabilizing liquid is sealed between the two diaphragms, and the diaphragm that receives the measured pressure is the outer diaphragm. The diaphragm of the original common diaphragm box is the inner diaphragm. When the outer diaphragm receives the pressure signal, this pressure is transmitted from the outer diaphragm to the ordinary diaphragm box by the silicone oil, thereby measuring the pressure felt by the outer diaphragm.
2. The diaphragm pressure sensor are mainly used for special measured medium. When the measured medium is a viscous liquid, it is easy to cause the common sensor to clog. Some of the measured media will crystallize after leaving the device. If we use a normal type sensor, the medium must be removed out, which usually causes the pressure guiding tube and the bellows chamber to become blocked, making it not working properly. Therefore, diaphragm pressure sensors must be used in the above cases.
3. The diaphragm pressure sensor has a remote transmission type (output signal RS485) and an integral type. The remote pressure sensor is a sensor whose outer diaphragm box and measurement diaphragm box are connected by enhanced capillary, and the capillary is generally 3-5 m. The outer diaphragm box is mounted on the device, and the inner diaphragm box as well as the sensor can be mounted on a bracket that is easy to maintain. Another form is that the outer diaphragm box and sensor are designed to be directly mounted on the device by flanges. Diaphragm pressure sensors can also be designed in a threaded connection, that is the outer diaphragm box or the outer elastic element can be placed in front of the mounting thread. As long as the internal threaded boss is welded to the measured device, the sensor can be screwed directly onto the device for easy installation.
- Classification of pressure sensors
The pressure sensors selection is usually considered in terms of installation conditions, environmental conditions, instrument performance, economy, and measurement medium. In practical applications, there are direct measurement and indirect measurement. Its uses include process measurement, process control and device interlocking. Most used pressure sensors are normal pressure sensors and differential pressure sensors.
- The difference between pressure sensor and differential pressure sensor
- In terms of meaning, the pressure sensor and the differential pressure sensor measure a certain pressure and the difference between two pressures, respectively, but they can measure much data indirectly. For example, in addition to measuring pressure, the pressure sensor can measure the liquid level in the device. When measuring the liquid level in the atmospheric pressure vessel, we can use a pressure sensor. When measuring the liquid level of a pressurized container, a differential pressure sensor is generally used. The pressure sensor can also be used to measure the medium density when the liquid level and pressure value in the container are constant. The measuring range of the pressure sensor can be designed to be very wide, starting from absolute pressure 0 to 100 MPa (general case).
- In addition to measuring the differential pressure of the two measured pressures, the differential pressure sensor can also measure the flow with various throttling elements. It can directly measure the liquid level in the pressurized container and the the atmospheric pressure vessel as well as the pressure and negative pressure.
-
How to select a diaphragm pressure sensor according practical application
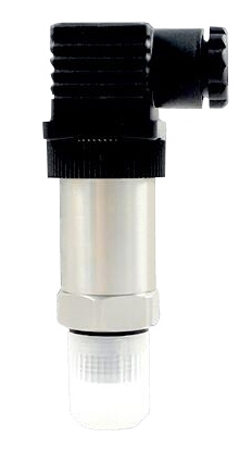
1. Structurally distinguish the pressure sensor and the differential pressure sensor, there are common type and diaphragm type. There is one measuring diaphragm in the common pressure sensor, which directly senses the pressure and differential pressure of the measured medium. The measuring diaphragm of the diaphragm pressure sensor receives the pressure of a stabilizing liquid (generally silicone oil), and the stabilizing liquid is sealed between the two diaphragms, and the diaphragm that receives the measured pressure is the outer diaphragm. The diaphragm of the original common diaphragm box is the inner diaphragm. When the outer diaphragm receives the pressure signal, this pressure is transmitted from the outer diaphragm to the ordinary diaphragm box by the silicone oil, thereby measuring the pressure felt by the outer diaphragm.
2. The diaphragm pressure sensor are mainly used for special measured medium. When the measured medium is a viscous liquid, it is easy to cause the common sensor to clog. Some of the measured media will crystallize after leaving the device. If we use a normal type sensor, the medium must be removed out, which usually causes the pressure guiding tube and the bellows chamber to become blocked, making it not working properly. Therefore, diaphragm pressure sensors must be used in the above cases.
3. The diaphragm pressure sensor has a remote transmission type (output signal RS485) and an integral type. The remote pressure sensor is a sensor whose outer diaphragm box and measurement diaphragm box are connected by enhanced capillary, and the capillary is generally 3-5 m. The outer diaphragm box is mounted on the device, and the inner diaphragm box as well as the sensor can be mounted on a bracket that is easy to maintain. Another form is that the outer diaphragm box and sensor are designed to be directly mounted on the device by flanges. Diaphragm pressure sensors can also be designed in a threaded connection, that is the outer diaphragm box or the outer elastic element can be placed in front of the mounting thread. As long as the internal threaded boss is welded to the measured device, the sensor can be screwed directly onto the device for easy installation.
- Pressure sensor selection according practical application
- The main basis for the pressure sensor or differential pressure sensor selection as the following: based on the property requirements of the measured medium, and saving money as well as facilitate installation and maintenance as a reference. If the measured medium is a material with high viscosity and strong corrode as well as easy to crystallize, a diaphragm pressure sensor must be used.
- When selecting a pressure sensor, the corrosion of the diaphragm box metal by the measured medium must be considered. Be sure to choose the material of the membrane box, otherwise the diaphragm will be corroded in a short time after use. Therefore, the material selection is the most important thing. The diaphragm of the pressure sensor is made of ordinary stainless steel, 304 stainless steel, 316L stainless steel and so on.
- In the pressure sensor selection, the measured medium temperature must be considered. If the temperature is higher than the normal medium temperature of 200-400 ° C, the high temperature pressure sensor should be used, otherwise the silicone oil will vaporize and expand, resulting in inaccurate measurement.
- The diaphragm pressure sensor is preferably in the form of a threaded connection, which saves money and is easy to install. For the selection of common pressure sensors and differential pressure sensors, the corrosiveness of the measured medium should also be considered. However, the medium temperature in use can be ignored, because in the normal pressure sensor, pressure is pressed into the watch, and the long-term working temperature is normal temperature, but the normal type uses a larger maintenance amount than the isolated type. Secondly, we must consider the insulation problem. Under the temperature conditions of below zero temperature in winter, the pressure guiding tube will freeze, causing the pressure sensor to not work and even damage. In this case, it is necessary to increase the heat tracing and incubator.
- From an economic point of view, when selecting a pressure sensor, as long as the measured medium is not a crystallization medium a normal type sensor can be used. Moreover, for low pressure and easy crystallization medium, it can also be indirectly measured by adding a purge medium (as long as the process allows the purge gas). The application of ordinary sensors requires maintenance personnel to carry out regular inspections, including whether various pressure guiding pipes are leaking, whether the purge medium is normal, whether the insulation is good, etc. As long as the maintenance work is done well, using a large number of ordinary sensors will save a lot of one-time investment.
- From the measurement range of the pressure sensor, generally the sensor have a certain range and adjustable range. Generally, the sensors have a certain range adjustable range. It is better to set the range to 1/4-3/4 of the range, so that the accuracy is guaranteed. Especially important for differential pressure sensors. In practice, some applications (such as liquid level measurement) need to migrate the measurement range of the pressure sensor. The measurement range and migration amount are calculated according to the site installation location, and the migration can be divided into positive migration and negative migration.