Industrial Pressure Sensor Application in Leak Detection
The pressure change leak detection method is to measure the total leak rate of the tested product by using the pressure change in the sealed container inside the tested product. According to the pressure types measured by the selected pressure sensor, the pressure change method is divided into vacuum pressure change method, differential pressure change method, and absolute pressure change method.
Vacuum pressure change method is suitable for long-term online seal leakage monitoring of double seal structures. For example, static seal leakage monitoring for the main structure of the space station.
The schematic diagram of the double sealing structure is shown in following figure. There are two leak paths in the course of its work. One is that the atmosphere outside the tested device leaks into the sealed cavity, and the other is that the sealed cavity leaks into the vacuum environment inside the tested device. The pressure change in the sealed chamber can be expressed by formula 1. By solving the differential equation expressed by equation 1, the relationship between the pressure change in the sealed cavity and the leak rate of the two seal rings can be obtained. The leak rate measurement can be finally achieved.
Formula 1 V×dPt=Q1-Q2
Pt is the instantaneous pressure in the sealed chamber, unit Pa; t is the measurement time, unit s; V is double sealing cavity volume, unit m3; Q1 is the leak rate of the seal ring 1, unit Pa·m3/s; Q2 is the leak rate of the seal ring 2, unit Pa·m3/s.
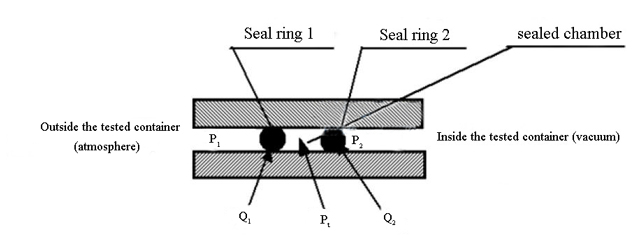
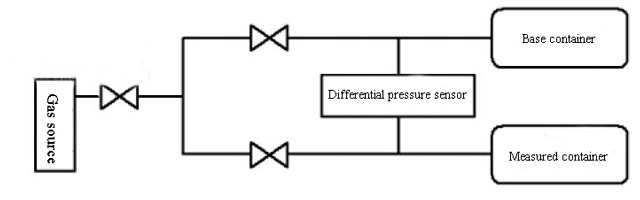
The advantage of the differential pressure change method is that the measurement sensitivity is high and the influence of the temperature change on the measurement result can be overcome. The disadvantage of this method is that the structure is complex and requires a dedicated measurement system. It should be noted that the volume of the base sealed container and the volume of the tested container should be as close as possible or close to each other to reduce the uncertainty of the measurement.
Absolute pressure change leak detection
Absolute pressure change method uses an absolute pressure sensor to achieve pressure measurement for the sealed container in the tested product. For the vacuum sealed container, after the exhausting is stopped, the measurement for the total leak rate of the tested product can be achieved by measuring the pressure rise value in a certain interval. For a pressurized container, the total leak rate measurement for the tested product can be achieved by measuring the pressure drop value at an interval after inflation.
The advantage of the absolute pressure change method is that the measurement method is simple and easy to operate. The disadvantage of this method is that the pressure in the tested container is affected by temperature greatly. When requiring accurate measurement for leak rate, temperature correction must be performed on the measurement results. However, for different structures of the tested containers, the law of pressure changes with temperature is not exactly the same, so a large number of experiments are needed to determine the correction method.
The absolute pressure change method is generally applied to the quantitative leak detection work in the vacuum system development process and the online leak detection in some special occasions. For example, the on-orbit detection for the sealing performance of the spacecraft hatch is achieved by the principle of absolute pressure change method.
Calculation formula for the general leak rate is as follows.
Q=∆P×V÷∆t
In the formula, Q is the total leak rate of the tested product, unit Pa·m3/s; ΔP is the amount of pressure change in the sealed container during the measurement time interval, unit Pa; V is the volume of the sealed container in the tested product, unit m3; Δt is the time interval in measurement, unit s.
In general, according to the state of increasing or decreasing pressure measured by pressure sensors, the pressure change method can be divided into static boosting method and static step-down method. If the pressure before the measurement interval is less than the pressure after the measurement interval, it is called static boost method. On the contrary, it is called static step-down method.
- The pressure sensor used in vacuum pressure changing leak detection
Vacuum pressure change method is suitable for long-term online seal leakage monitoring of double seal structures. For example, static seal leakage monitoring for the main structure of the space station.
The schematic diagram of the double sealing structure is shown in following figure. There are two leak paths in the course of its work. One is that the atmosphere outside the tested device leaks into the sealed cavity, and the other is that the sealed cavity leaks into the vacuum environment inside the tested device. The pressure change in the sealed chamber can be expressed by formula 1. By solving the differential equation expressed by equation 1, the relationship between the pressure change in the sealed cavity and the leak rate of the two seal rings can be obtained. The leak rate measurement can be finally achieved.
Formula 1 V×dPt=Q1-Q2
Pt is the instantaneous pressure in the sealed chamber, unit Pa; t is the measurement time, unit s; V is double sealing cavity volume, unit m3; Q1 is the leak rate of the seal ring 1, unit Pa·m3/s; Q2 is the leak rate of the seal ring 2, unit Pa·m3/s.
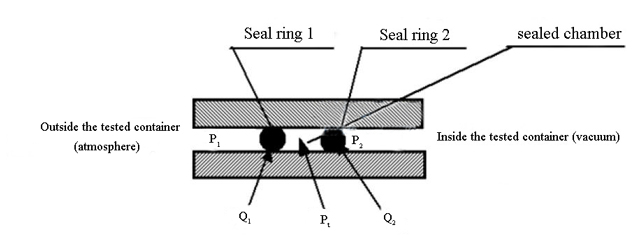
- Differential pressure sensor used in differential pressure changing leak detection
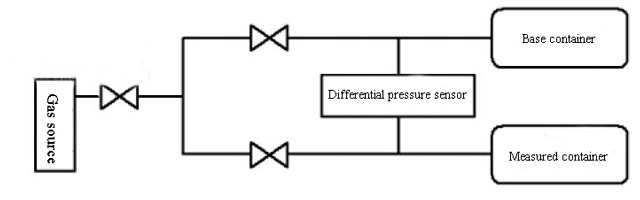
The advantage of the differential pressure change method is that the measurement sensitivity is high and the influence of the temperature change on the measurement result can be overcome. The disadvantage of this method is that the structure is complex and requires a dedicated measurement system. It should be noted that the volume of the base sealed container and the volume of the tested container should be as close as possible or close to each other to reduce the uncertainty of the measurement.
Absolute pressure change leak detection
Absolute pressure change method uses an absolute pressure sensor to achieve pressure measurement for the sealed container in the tested product. For the vacuum sealed container, after the exhausting is stopped, the measurement for the total leak rate of the tested product can be achieved by measuring the pressure rise value in a certain interval. For a pressurized container, the total leak rate measurement for the tested product can be achieved by measuring the pressure drop value at an interval after inflation.
The advantage of the absolute pressure change method is that the measurement method is simple and easy to operate. The disadvantage of this method is that the pressure in the tested container is affected by temperature greatly. When requiring accurate measurement for leak rate, temperature correction must be performed on the measurement results. However, for different structures of the tested containers, the law of pressure changes with temperature is not exactly the same, so a large number of experiments are needed to determine the correction method.
The absolute pressure change method is generally applied to the quantitative leak detection work in the vacuum system development process and the online leak detection in some special occasions. For example, the on-orbit detection for the sealing performance of the spacecraft hatch is achieved by the principle of absolute pressure change method.
Calculation formula for the general leak rate is as follows.
Q=∆P×V÷∆t
In the formula, Q is the total leak rate of the tested product, unit Pa·m3/s; ΔP is the amount of pressure change in the sealed container during the measurement time interval, unit Pa; V is the volume of the sealed container in the tested product, unit m3; Δt is the time interval in measurement, unit s.
In general, according to the state of increasing or decreasing pressure measured by pressure sensors, the pressure change method can be divided into static boosting method and static step-down method. If the pressure before the measurement interval is less than the pressure after the measurement interval, it is called static boost method. On the contrary, it is called static step-down method.