Pressure Sensor Applications in 3 Major Industrial Fields
In all various of industries, applications of the pressure sensor are more and more wide. In the petrochemical industry, especially in large-scale chemical projects, pressure sensors are one of the most used measuring devices for automatic control equipment. In water and wastewater treatment processes, pressure sensors provide an important means of control and monitoring for system protection and quality assurance.
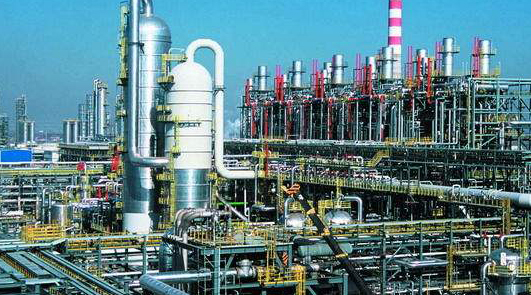
Corresponding to the measurement accuracy of the pressure transducer is the measurement accuracy and response speed of the pressure sensor, Corresponding to the stability of the pressure transducer is the temperature and static pressure characteristics of the pressure sensor and long-term stability. The demand for pressure sensors in the petrochemical industry is reflected in measurement accuracy, rapid response, temperature characteristics, static pressure characteristics, and long-term stability.
The pressure sensor converts the pressure into an electrical output signal, which can be used to measure the level of the static fluid, so it can be used to measure the liquid level. The sensitive components of the pressure sensor are mainly composed of a silicon cup type force sensitive component, silicone oil, an isolating diaphragm and an gas guiding tube. The pressure P of the measured medium is transmitted to one side of the silicon cup element through the isolating diaphragm and silicone oil (see in figure), The atmospheric reference pressure po acts on the other side of the silicon cup element through the gas guiding tube. The silicon cup component is a cup-shaped monocrystalline silicon wafer whose bottom is processed very thin. The diaphragm of the bottom of the cup produces elastic deformation with minimal displacement under the action of pressure P and Po. Monocrystalline silicon is an ideal elastomer, whose deformation is strictly proportional to the pressure, and its recovery performance is excellent.
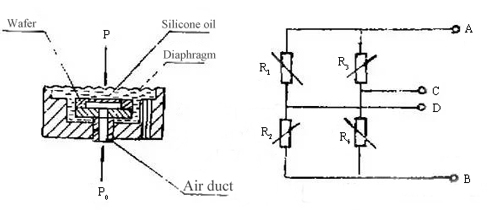
On the silicon diaphragm, four bridge resistors that formed by semiconductor diffusion process are arranged in a square shape, When the silicon diaphragm is deformed by pressure, the two resistors on the diagonal are forced by compressive stress, and the other two resistors are forced by tensile stress. Due to the piezoresistive effect of the diffused silicon, the resistance of the two opposing resistors increases, while the resistance of the other two resistors decreases. If added voltage to both ends of A-B, there will be a voltage output signal between C-D that is proportional to P-Po differential pressure.
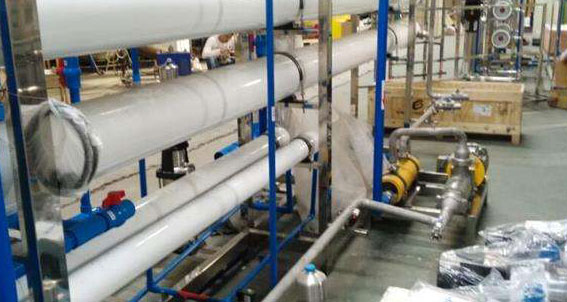
Under a proper pressure, the gas can be pressed into a small space. As the pressure increases, the pressure of the gas in the space gradually increases, and the gas is compressed. Conversely, if a certain amount of gas is pressed into a space whose occupied volume is larger than that in ordinary situation, the gas always fills the space evenly. The pressure there will be lower than the pressure of the charged original gas, so the gas expands. The gas has no fixed shape and its volume is also determined by the volume of the container. Therefore, when discussing and studying the mechanical problems about gases, it is not enough to mention the weight of it. It is often necessary to mention the volume of it. Severity is a physical quantity indicating the weight of a gas contained in a unit volume.
For gas pressure measurement, ATO provides a solution using a pressure sensor to achieve the meaning of measurement. A pressure sensor for gas pressure measurement is mainly a conversion device for measuring the absolute pressure of a gas, which can be used for pressure measurement in steam, air, wind and pipeline. Its performance is stable and reliable, and can be applied to physical experiments related to gas pressure, such as gas law as well as can also measure the pressure of dry, non-corrosive gases in biological and chemical experiments.
- Applications of the pressure sensor in the petrochemical industry
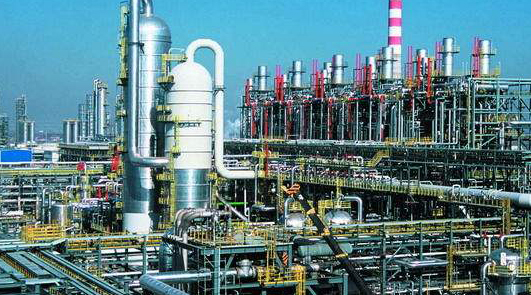
Corresponding to the measurement accuracy of the pressure transducer is the measurement accuracy and response speed of the pressure sensor, Corresponding to the stability of the pressure transducer is the temperature and static pressure characteristics of the pressure sensor and long-term stability. The demand for pressure sensors in the petrochemical industry is reflected in measurement accuracy, rapid response, temperature characteristics, static pressure characteristics, and long-term stability.
- In the production process of the petrochemical industry, safe, stable and reliable pressure sensors are powerful tools to ensure the production process. Once the measurement error occurs, failures and downtimes are prone to occur, resulting in very large economic losses. Therefore, stability is the most basic requirement for pressure sensors in the petroleum industry.
- During the pressure measurement process, the pressure sensor will drift as the working environment changes and the static pressure changes. It is most evident in the micro differential pressure measurement process. Pressure sensors should have the ability to work in different environments without drifting due to environmental changes. This is also the key to ensuring the continuity of the production process.
- The petrochemical industry belongs to the precision industry and has very high requirements for the measurement accuracy of pressure sensors. In the entire control system, the higher the accuracy of the measured values, the better the control effect.
- Applications of the pressure sensor in water treatment
The pressure sensor converts the pressure into an electrical output signal, which can be used to measure the level of the static fluid, so it can be used to measure the liquid level. The sensitive components of the pressure sensor are mainly composed of a silicon cup type force sensitive component, silicone oil, an isolating diaphragm and an gas guiding tube. The pressure P of the measured medium is transmitted to one side of the silicon cup element through the isolating diaphragm and silicone oil (see in figure), The atmospheric reference pressure po acts on the other side of the silicon cup element through the gas guiding tube. The silicon cup component is a cup-shaped monocrystalline silicon wafer whose bottom is processed very thin. The diaphragm of the bottom of the cup produces elastic deformation with minimal displacement under the action of pressure P and Po. Monocrystalline silicon is an ideal elastomer, whose deformation is strictly proportional to the pressure, and its recovery performance is excellent.
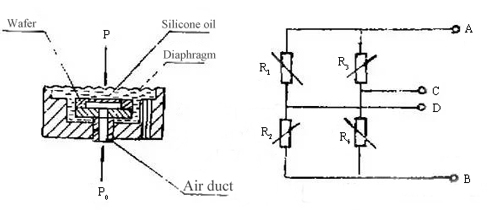
On the silicon diaphragm, four bridge resistors that formed by semiconductor diffusion process are arranged in a square shape, When the silicon diaphragm is deformed by pressure, the two resistors on the diagonal are forced by compressive stress, and the other two resistors are forced by tensile stress. Due to the piezoresistive effect of the diffused silicon, the resistance of the two opposing resistors increases, while the resistance of the other two resistors decreases. If added voltage to both ends of A-B, there will be a voltage output signal between C-D that is proportional to P-Po differential pressure.
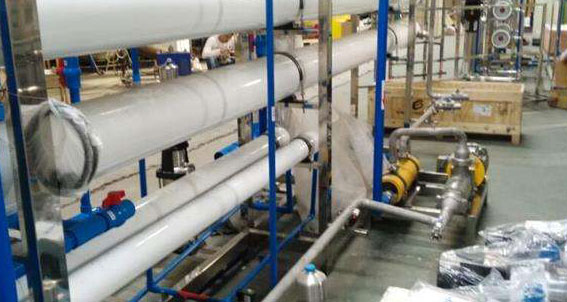
- Applications of the pressure sensor in air pressure measurement
Under a proper pressure, the gas can be pressed into a small space. As the pressure increases, the pressure of the gas in the space gradually increases, and the gas is compressed. Conversely, if a certain amount of gas is pressed into a space whose occupied volume is larger than that in ordinary situation, the gas always fills the space evenly. The pressure there will be lower than the pressure of the charged original gas, so the gas expands. The gas has no fixed shape and its volume is also determined by the volume of the container. Therefore, when discussing and studying the mechanical problems about gases, it is not enough to mention the weight of it. It is often necessary to mention the volume of it. Severity is a physical quantity indicating the weight of a gas contained in a unit volume.
For gas pressure measurement, ATO provides a solution using a pressure sensor to achieve the meaning of measurement. A pressure sensor for gas pressure measurement is mainly a conversion device for measuring the absolute pressure of a gas, which can be used for pressure measurement in steam, air, wind and pipeline. Its performance is stable and reliable, and can be applied to physical experiments related to gas pressure, such as gas law as well as can also measure the pressure of dry, non-corrosive gases in biological and chemical experiments.