How to Protect Pressure Sensor from Interference
Generally, both the pressure sensor and the measured medium are inevitably affected by external interference factors, so they are in the interfered environment at the same time. Because the pressure sensor acquires relevant information by direct or indirect contact with the measurement medium. This requires some anti-interference methods to improve the anti- interference capability of the pressure sensor. If the anti-interference ability of the pressure sensor is not too hard, its application range will be greatly limited, and the use value will greatly reduce. Therefore, research and mastering the anti- interference methods for pressure sensors is a problem that cannot be ignored.
Most pressure sensors will zero drift after overtime work, so it is important to understand the stability of the pressure sensor before purchasing. This pre-work can reduce the hassle in future use.
2. The package of the pressure sensor
The package of the sensor, especially often be ignored, is its frame, but this will gradually reveal its shortcomings in later use. In the pressure sensor selection, be sure to consider its future working environment, humidity and installation method as well as whether there will be strong impact or vibration.
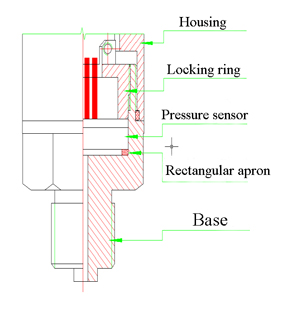
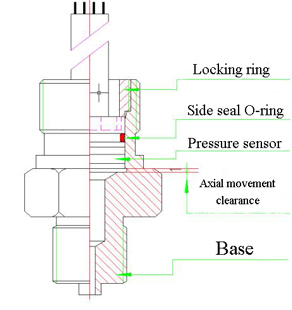
3. Select output signal for the pressure sensor
What kind of output signals the pressure sensor needs to get: mV, V, mA and frequency output, digital output, depending on various factors, including the distance between the pressure sensor and the system controller or display, whether there is noise or other electronic interference signals,whether the amplifier are needed and the position of the amplifier, etc. For many OEM equipment with short distances between pressure sensors and controllers, sensors with mA output are the most economical and effective solution; if you need to amplify the output signal, it is best to use a pressure sensor with built-in amplification. For long-distance transmission or strong electrical interference signals, it is best to use mA output or frequency output.
In environments with high RFI or EMI specifications, in addition to it is need to select mA or frequency output, special protection or filters are also considered. In order to meet different measurement needs, there are many kinds of output signals of pressure sensors on the market, mainly 4-20mA, 0-20mA, 0-10V, 0-5V and so on. The most commonly used are 4-20mA and 0-10V. In the output signals listed above, only 0-20 mA is a two-wire system, and the others are all three-wire systems. The so-called output is a several wire do not contain ground or shielded wires.
4. Select excitation voltage
The type of output signal determine which excitation voltage is selected. Many amplification sensors have built-in voltage regulation, so the range of their supply voltage is large. Some pressure sensors are quantitatively configured and require a stable operating voltage. Therefore, the available operating voltage determines whether or not to use a pressure sensor with a regulator. When selecting a pressure sensor, it is necessary to consider the operating voltage and system cost.
5. Confirm if it is need to have interchangeable pressure sensors
Determine if the required pressure sensor can accommodate multiple use systems. In general, this is important, especially for OEM products. Once the product are delivered to the customer, the cost for the customer to calibrate is considerable.
6. Others
After confirming some of the above parameters, we must also confirm the process connection interface of your pressure sensor and the supply voltage; if it is used in special occasions, also needs to consider the explosion protection and protection level.
-
Several main interference phenomena to the pressure sensor
- When the pressure sensor issue a command, the motor rotates irregularly.
- When the signal is zero, the value of the digital display numerical jump.
- When the pressure sensor is working, its output value does not match the signal value corresponding to the actual parameter, and the error value is random and irregular.
- When the measured parameter is stable, the difference between the value of the pressure sensor output and the signal value corresponding to the measured parameter is a stable value or a periodically varying value.
- Devices (such as monitors) that share the same power supply with the AC servo system do not work properly.
- Two channels for the interference to enter the positioning control system
- Signal transmission channel. Interference enter through the signal input and output channels associated with the system. The signal transmission channel is the way the control system or driver receives the feedback signal and sends out the control signal. Because the pulse wave will have delay, distortion, attenuation and channel interference on the transmission line, the long-line interference is the main factor in the transmission process.
- Power supply system. There are internal resistances in any power supply and transmission lines. It is these internal resistances that cause noise interference from the power supply. If there is no internal resistance, no matter what kind of noise will be absorbed by the short circuit of the power supply, no interference voltage will be established in the line. In addition, the drive of the AC servo system itself is also a strong source of interference, which can interfere other devices through the power supply.
- Anti-interference method
Most pressure sensors will zero drift after overtime work, so it is important to understand the stability of the pressure sensor before purchasing. This pre-work can reduce the hassle in future use.
2. The package of the pressure sensor
The package of the sensor, especially often be ignored, is its frame, but this will gradually reveal its shortcomings in later use. In the pressure sensor selection, be sure to consider its future working environment, humidity and installation method as well as whether there will be strong impact or vibration.
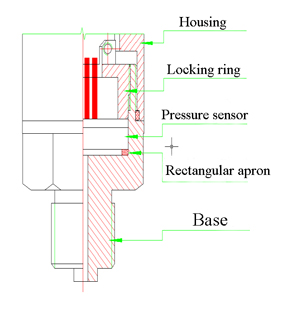
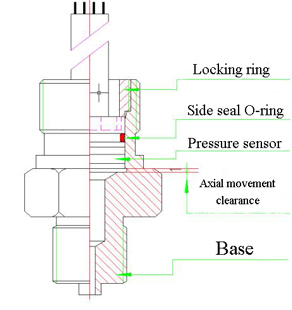
3. Select output signal for the pressure sensor
What kind of output signals the pressure sensor needs to get: mV, V, mA and frequency output, digital output, depending on various factors, including the distance between the pressure sensor and the system controller or display, whether there is noise or other electronic interference signals,whether the amplifier are needed and the position of the amplifier, etc. For many OEM equipment with short distances between pressure sensors and controllers, sensors with mA output are the most economical and effective solution; if you need to amplify the output signal, it is best to use a pressure sensor with built-in amplification. For long-distance transmission or strong electrical interference signals, it is best to use mA output or frequency output.
In environments with high RFI or EMI specifications, in addition to it is need to select mA or frequency output, special protection or filters are also considered. In order to meet different measurement needs, there are many kinds of output signals of pressure sensors on the market, mainly 4-20mA, 0-20mA, 0-10V, 0-5V and so on. The most commonly used are 4-20mA and 0-10V. In the output signals listed above, only 0-20 mA is a two-wire system, and the others are all three-wire systems. The so-called output is a several wire do not contain ground or shielded wires.
4. Select excitation voltage
The type of output signal determine which excitation voltage is selected. Many amplification sensors have built-in voltage regulation, so the range of their supply voltage is large. Some pressure sensors are quantitatively configured and require a stable operating voltage. Therefore, the available operating voltage determines whether or not to use a pressure sensor with a regulator. When selecting a pressure sensor, it is necessary to consider the operating voltage and system cost.
5. Confirm if it is need to have interchangeable pressure sensors
Determine if the required pressure sensor can accommodate multiple use systems. In general, this is important, especially for OEM products. Once the product are delivered to the customer, the cost for the customer to calibrate is considerable.
6. Others
After confirming some of the above parameters, we must also confirm the process connection interface of your pressure sensor and the supply voltage; if it is used in special occasions, also needs to consider the explosion protection and protection level.