What Affect Measurement Accuracy in Pressure Sensor Application
In the pressure sensor application, there are many factors that affecting the measurement accuracy. Due to the overall design of the industrial site, the pressure sensor can not be installed near the measuring point in the use site, but is pressed to a more concentrated place through the pressure pipe to facilitate maintenance and management. This will result in a height difference between the measuring point and the mounting point. The pressure transmitting medium in the pressure pipe will generate additional pressure due to the height difference, which will introduce additional errors, thus affecting the measurement accuracy. In the application of industrial processes, since the density of the measured medium is often large, even with a small height difference, the additional error introduced is large.
With the advancement of instrument technology, pressure sensors are moving toward high accuracy and intelligence. However, advances in technology have created a misunderstanding for designers, that is, when choosing a pressure sensor, people tend to pay attention to its own accuracy, while ignoring other factors that affect measurement accuracy. In fact, what the user really needs is that the pressure sensor can correctly reflect the true value of the measured value, that is, the measurement accuracy, rather than the accuracy of the pressure sensor itself. There are many factors that affect the accuracy of pressure sensor measurement. Some factors are related to environmental conditions and installation methods. Therefore, the accuracy of the product itself does not guarantee the actual measurement results during design. When selecting the pressure sensor, users should not only consider the impact of the actual environment on the accuracy of the product, but also should minimize the impact on accuracy during installation. So, what factors affect the pressure sensor?
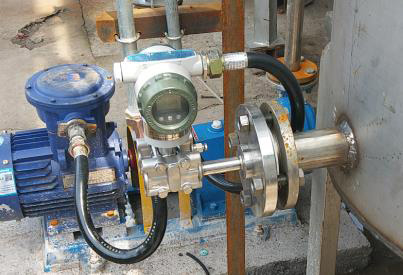
In the differential pressure measurement, the measuring element senses the pressure difference between the two sides by the deformation displacement of the measuring diaphragm at the measuring center. Since the central measuring chamber is filled with the filling silicone oil, when the pressure sensor is tilted in a horizontal direction perpendicular to the measuring diaphragm, the filling silicone oil itself exerts pressure on the measuring diaphragm. This pressure causes the diaphragm to deform, resulting in a change in the output value. When the pressure sensor is tilted in a direction parallel to the plane of the measuring diaphragm, the filling silicone oil does not force the measuring diaphragm, and thus does not affect. For pressure sensors with different ranges, degree of influence affected by the angle of inclination are different. The smaller the range, the greater the impact. When the pressure sensor is tilted forward and backward, the output linearity and output value change is not obvious and will not affect its normal use. When the pressure sensor is tilted to the left or right, its output value will drift in one direction according to the tilt angle. The larger the angle, the greater the impact, but the linearity does not change significantly.
For most of the pressure sensor, when the range ratio is in the range of 10:1, the accuracy is still the reference accuracy and is not affected by the range ratio. However, there are still a considerable number of pressure sensors with a range ratio of less than 10:1 if guarantee a reference accuracy. Moreover, for the different range codes of the same model, the range ratio of the reference accuracy will be greatly different. These are especially important when the user is calculating the accuracy affected by the range ratio.
With the advancement of instrument technology, pressure sensors are moving toward high accuracy and intelligence. However, advances in technology have created a misunderstanding for designers, that is, when choosing a pressure sensor, people tend to pay attention to its own accuracy, while ignoring other factors that affect measurement accuracy. In fact, what the user really needs is that the pressure sensor can correctly reflect the true value of the measured value, that is, the measurement accuracy, rather than the accuracy of the pressure sensor itself. There are many factors that affect the accuracy of pressure sensor measurement. Some factors are related to environmental conditions and installation methods. Therefore, the accuracy of the product itself does not guarantee the actual measurement results during design. When selecting the pressure sensor, users should not only consider the impact of the actual environment on the accuracy of the product, but also should minimize the impact on accuracy during installation. So, what factors affect the pressure sensor?
- Static pressure affecting the pressure sensor accuracy
- Tilt angle in installation affecting the pressure sensor accuracy
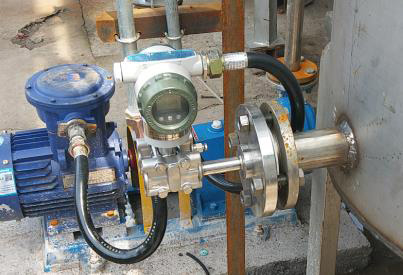
In the differential pressure measurement, the measuring element senses the pressure difference between the two sides by the deformation displacement of the measuring diaphragm at the measuring center. Since the central measuring chamber is filled with the filling silicone oil, when the pressure sensor is tilted in a horizontal direction perpendicular to the measuring diaphragm, the filling silicone oil itself exerts pressure on the measuring diaphragm. This pressure causes the diaphragm to deform, resulting in a change in the output value. When the pressure sensor is tilted in a direction parallel to the plane of the measuring diaphragm, the filling silicone oil does not force the measuring diaphragm, and thus does not affect. For pressure sensors with different ranges, degree of influence affected by the angle of inclination are different. The smaller the range, the greater the impact. When the pressure sensor is tilted forward and backward, the output linearity and output value change is not obvious and will not affect its normal use. When the pressure sensor is tilted to the left or right, its output value will drift in one direction according to the tilt angle. The larger the angle, the greater the impact, but the linearity does not change significantly.
- Temperature affecting the pressure sensor accuracy
- Range ratio affecting the pressure sensor accuracy
For most of the pressure sensor, when the range ratio is in the range of 10:1, the accuracy is still the reference accuracy and is not affected by the range ratio. However, there are still a considerable number of pressure sensors with a range ratio of less than 10:1 if guarantee a reference accuracy. Moreover, for the different range codes of the same model, the range ratio of the reference accuracy will be greatly different. These are especially important when the user is calculating the accuracy affected by the range ratio.