Select What Pressure Sensor for Nuclear Power Plant Application
This paper introduces the pressure sensor selection for nuclear power plant application. Combined with the technical requirements to pressure sensors for nuclear power plants, the paper gives the selection methods and precautions to provide reference for the selection and design of pressure sensors to nuclear power plants.
For nuclear power plants, the process detection instrument is the interface between the entire instrument control system and the process. The performance of the instrument directly affects the performance of the instrument control system. For various process instruments, the pressure sensor is the most wide and common in use. It is mainly used to detect the pressure, flow and liquid level for the process system. Pressure sensors provide the necessary signals for nuclear power plant protection systems and post-accident monitoring systems for safety protection and post-accident monitoring. Therefore, the correct and reasonable selection for pressure sensors is very important to ensure the safe and reliable operation of nuclear power plants.
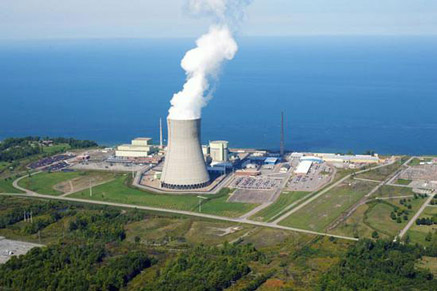
1. According to the type of measured pressure
The pressure sensor can be divided into gauge pressure sensor, Differential pressure sensor and absolute pressure sensor.
2. According to the measurement principle
The pressure sensors commonly used in nuclear power plants can be divided into: monocrystalline silicon pressure sensors, diffused silicon pressure sensors, differential pressure sensors, varistor pressure sensors, inductive displacement pressure sensors, and force balance sensors.
3. According to whether to measure the medium directly
The pressure sensor can be divided into basic pressure sensor and flange sensor with a remote capillary.
4. According to the function
According to whether the instrument performs safety function, the pressure sensor in nuclear power plant can be divided into safety level pressure sensor and non-safety level pressure sensor. Safety level pressure sensors should be calibrated by different qualification requirements to ensure proper functioning when required.
1. Safety Level of the pressure sensor
The safe operation of a nuclear power plant depends primarily on the reliability of the equipment that performing the safety function. Some electrical equipment whose safety functions are emergency shutdown, emergency core cooling, waste heat exhausting, safety shell isolation, safety shell heat rejection and preventing the release of radioactive materials into the environment. We called this equipment Safety (1E) grade electrical equipment. Especially for the pressure sensor or differential pressure sensor installed at the safety shell in nuclear power plants, which operate in an radiated environment with very harsh working conditions and require maintaining its function and performance under seismic and accident conditions such as LOCA accidents. In order to ensure that the pressure sensor can adapt to the most demanding environmental conditions and perform the specified safety functions under various operating conditions in the nuclear power plant during its service life, it is necessary to use a quality-qualified sensor product.
For some instruments that need to send signals to the post-accident monitoring system and protection system, the selection shall be in accordance with the requirements of the RCC-E for K1, K2, and K3 instruments (some of which may be equivalent to IEEE-323/344) and then select the proper instrument.
For the pressure sensors that must be used in serious accidents, the pressure sensor should be qualified according to the technical requirements or analyzed with certain credibility to prove that it can withstand severe accident environmental conditions and be available during and after the accident.
2. The types and measurement range of the pressure sensor
According to the process specifications requirements and the measured pressure types, select the corresponding pressure sensor, differential pressure sensor or absolute pressure sensor, and the working pressure level of the equipment and the working pressure level of the sensor should be considered in the selection.
When measuring steady pressure, the pressure sensor range is generally selected to be close to or slightly 1.5 times the normal pressure value. When measuring the pulsating pressure, the pressure sensor range is generally selected to be close to or slightly 2 times the normal pressure value, and considering the sensor's overrange overload capability. When measuring the pump outlet pressure, generally the selected maximum range is close to the maximum pressure at the pump outlet. When measuring high pressure, generally the selected maximum range is greater than 1.7 times the maximum measured pressure.
The measurement range must be within the pressure sensor range and must not be lower than the minimum range. Especially in applications where the differential pressure is used to measure the liquid level, the differential pressure sensor range after migration should not exceed the maximum range (URL) of the sensor, otherwise it will not be accurately measured. When selecting a differential pressure sensor, the influence of static pressure resistance and effect of static pressure on measurement accuracy should be considered.
3. Choose the right material
According to the physical and chemical properties of the measured medium, select the wetted part (process interface) of the pressure sensor and the material of the non-contact part and the isolating diaphragm. For the part in contact with the medium, the sensor material should meet the requirements of the RCC series standards, and processed with the austenitic ultra-low carbon stainless steel material. Currently, commonly used stainless steel materials are 304L or 316L (ASTM standard). Systems involving seawater media should select the Hastelloy C with corrosion-resistant ability.
In the actual selection process, some special treatments will be made due to the different structure of the pressure sensor itself. For example, the venting part of the pressure sensor is a needle valve, and if the sealing steel ball is also 316L, it will be disadvantageous to the sealing surface after multiple venting operations.
4. Operation and maintenance requirements for the pressure sensor
The selection of pressure sensor and differential pressure sensor should consider the control channel requirements, and select the instrument with higher accuracy according to the control performance requirements. For the instrument in the test instrument system which is used for heat balance calculation, the pressure sensor and the differential pressure sensor with better accuracy and performance should be selected according to the accuracy requirements. In addition to this, the convenience of maintenance should be considered. Taking into account the radiation protection zone, the instrument should be placed in the area where the personnel can reach, installed on the instrument frame for convenient maintenance and operation, and meet the requirements for periodic tests and instrument calibration requirements.
5. Other considerations
In the pressure sensor selection for nuclear power plants, the requirements to functional accuracy, response time, accuracy after accident, consistency, etc. for special measuring points should also be considered. In addition, if the environment in which the instrument is located is present in the presence of flammable and explosive gases, explosion protection is required. Some instruments are non-security level in the electrical equipment classification list, but there are requirements of performing functions under earthquake conditions for the instrument, or the radiation zone in the installation location has a certain irradiation dose. In this type of selection, in order to ensure the measurement accuracy and stability of the pressure sensor in long-term work, it is usually considered to select a pressure sensor that has been subjected to irradiation aging and seismic tests.
For nuclear power plants, the process detection instrument is the interface between the entire instrument control system and the process. The performance of the instrument directly affects the performance of the instrument control system. For various process instruments, the pressure sensor is the most wide and common in use. It is mainly used to detect the pressure, flow and liquid level for the process system. Pressure sensors provide the necessary signals for nuclear power plant protection systems and post-accident monitoring systems for safety protection and post-accident monitoring. Therefore, the correct and reasonable selection for pressure sensors is very important to ensure the safe and reliable operation of nuclear power plants.
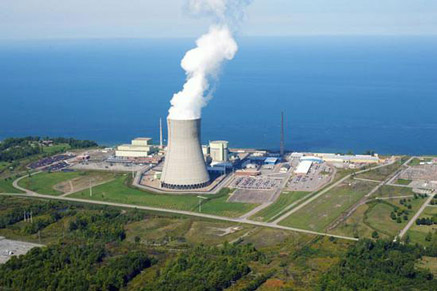
- The pressure sensor types in the nuclear power plant
1. According to the type of measured pressure
The pressure sensor can be divided into gauge pressure sensor, Differential pressure sensor and absolute pressure sensor.
2. According to the measurement principle
The pressure sensors commonly used in nuclear power plants can be divided into: monocrystalline silicon pressure sensors, diffused silicon pressure sensors, differential pressure sensors, varistor pressure sensors, inductive displacement pressure sensors, and force balance sensors.
3. According to whether to measure the medium directly
The pressure sensor can be divided into basic pressure sensor and flange sensor with a remote capillary.
4. According to the function
According to whether the instrument performs safety function, the pressure sensor in nuclear power plant can be divided into safety level pressure sensor and non-safety level pressure sensor. Safety level pressure sensors should be calibrated by different qualification requirements to ensure proper functioning when required.
- The pressure sensor design principle in nuclear power plant
- Meet the standard specification requirements in the design, manufacture, inspection and quality appraisal for pressure sensors in nuclear power plants.
- Meet the measurement requirements in the process system to this type of instrument.
- Meet the special requirements for this type of instrument in nuclear power plant safety function, safety analysis, and accident management.
- Convenient to install and maintain the instrument。
- Adapt to the requirements for subsequent power plant equipment transformation, minimize the type of instrument and facilitate maintenance.
- The pressure sensor selection for nuclear power plants
1. Safety Level of the pressure sensor
The safe operation of a nuclear power plant depends primarily on the reliability of the equipment that performing the safety function. Some electrical equipment whose safety functions are emergency shutdown, emergency core cooling, waste heat exhausting, safety shell isolation, safety shell heat rejection and preventing the release of radioactive materials into the environment. We called this equipment Safety (1E) grade electrical equipment. Especially for the pressure sensor or differential pressure sensor installed at the safety shell in nuclear power plants, which operate in an radiated environment with very harsh working conditions and require maintaining its function and performance under seismic and accident conditions such as LOCA accidents. In order to ensure that the pressure sensor can adapt to the most demanding environmental conditions and perform the specified safety functions under various operating conditions in the nuclear power plant during its service life, it is necessary to use a quality-qualified sensor product.
For some instruments that need to send signals to the post-accident monitoring system and protection system, the selection shall be in accordance with the requirements of the RCC-E for K1, K2, and K3 instruments (some of which may be equivalent to IEEE-323/344) and then select the proper instrument.
For the pressure sensors that must be used in serious accidents, the pressure sensor should be qualified according to the technical requirements or analyzed with certain credibility to prove that it can withstand severe accident environmental conditions and be available during and after the accident.
2. The types and measurement range of the pressure sensor
According to the process specifications requirements and the measured pressure types, select the corresponding pressure sensor, differential pressure sensor or absolute pressure sensor, and the working pressure level of the equipment and the working pressure level of the sensor should be considered in the selection.
When measuring steady pressure, the pressure sensor range is generally selected to be close to or slightly 1.5 times the normal pressure value. When measuring the pulsating pressure, the pressure sensor range is generally selected to be close to or slightly 2 times the normal pressure value, and considering the sensor's overrange overload capability. When measuring the pump outlet pressure, generally the selected maximum range is close to the maximum pressure at the pump outlet. When measuring high pressure, generally the selected maximum range is greater than 1.7 times the maximum measured pressure.
The measurement range must be within the pressure sensor range and must not be lower than the minimum range. Especially in applications where the differential pressure is used to measure the liquid level, the differential pressure sensor range after migration should not exceed the maximum range (URL) of the sensor, otherwise it will not be accurately measured. When selecting a differential pressure sensor, the influence of static pressure resistance and effect of static pressure on measurement accuracy should be considered.
3. Choose the right material
According to the physical and chemical properties of the measured medium, select the wetted part (process interface) of the pressure sensor and the material of the non-contact part and the isolating diaphragm. For the part in contact with the medium, the sensor material should meet the requirements of the RCC series standards, and processed with the austenitic ultra-low carbon stainless steel material. Currently, commonly used stainless steel materials are 304L or 316L (ASTM standard). Systems involving seawater media should select the Hastelloy C with corrosion-resistant ability.
In the actual selection process, some special treatments will be made due to the different structure of the pressure sensor itself. For example, the venting part of the pressure sensor is a needle valve, and if the sealing steel ball is also 316L, it will be disadvantageous to the sealing surface after multiple venting operations.
4. Operation and maintenance requirements for the pressure sensor
The selection of pressure sensor and differential pressure sensor should consider the control channel requirements, and select the instrument with higher accuracy according to the control performance requirements. For the instrument in the test instrument system which is used for heat balance calculation, the pressure sensor and the differential pressure sensor with better accuracy and performance should be selected according to the accuracy requirements. In addition to this, the convenience of maintenance should be considered. Taking into account the radiation protection zone, the instrument should be placed in the area where the personnel can reach, installed on the instrument frame for convenient maintenance and operation, and meet the requirements for periodic tests and instrument calibration requirements.
5. Other considerations
In the pressure sensor selection for nuclear power plants, the requirements to functional accuracy, response time, accuracy after accident, consistency, etc. for special measuring points should also be considered. In addition, if the environment in which the instrument is located is present in the presence of flammable and explosive gases, explosion protection is required. Some instruments are non-security level in the electrical equipment classification list, but there are requirements of performing functions under earthquake conditions for the instrument, or the radiation zone in the installation location has a certain irradiation dose. In this type of selection, in order to ensure the measurement accuracy and stability of the pressure sensor in long-term work, it is usually considered to select a pressure sensor that has been subjected to irradiation aging and seismic tests.