What is Long Term Stability of Pressure Sensor
Factors such as temperature and mechanical stress will have negative impact on the long-term stability of the pressure sensor. However, in the production process, users can minimize the impact by regular testing. Manufacturers usually specify the long-term stability of the pressure sensor in a data sheet. The values given in these data sheets are determined under laboratory conditions, which refer to the expected maximum change in the zero point and output range throughout the year. For example, a long-term stability of ≤0.2% FS/year means that the total error of the pressure sensor will decrease by 0.2% of the total scale within one year. Pressure sensors usually take some time to "stabilize". As mentioned earlier, the zero point and sensitivity (output signal) are the main factors mentioned here. Users often notice the zero drift of the pressure sensor as they are easy to identify and adjust.
Nevertheless, it is impossible for pressure sensors to have unlimited long-term stability and accuracy. Factors such as pressure hysteresis and temperature hysteresis cannot be completely eliminated. It can be said that they are characteristics of a pressure sensor. Users can make corresponding plans. For example, for high accuracy applications, the pressure hysteresis and temperature hysteresis should not exceed 0.02% of the total scale. In addition, the physics law have certain limitations on the long-term stability of pressure sensors. Wear and tear testing is required in particularly demanding applications such as wave and high temperature applications. For normal pressure sensors, a continuous high temperature of over 150 ℃ eventually destroys the pressure sensor.
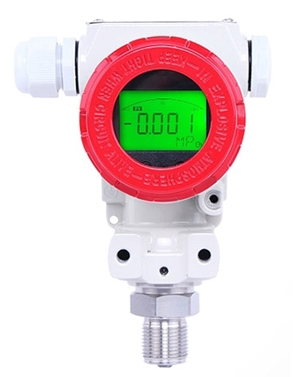
In order to achieve the best long-term stability for the pressure sensor, that is, only a minor displacement occurs during the life of the product. The core component that is the sensor chip must be correct. For a diffused silicon pressure sensor, it uses a diffused silicon core as the core component. Pressure sensors with good stability have already begun to lay the foundation in the production process. Therefore, sufficient silicon chip identification is vital for producing long-term stable pressure sensors. The assembly of the pressure sensor is also decisive. The silicon wafer is glued to the outer casing. Due to factors such as temperature, the material sticking to the chip will move, which affects the mechanical stress on the chip. The result of this is that the measurement results are becoming more and more inaccurate. Practice has shown that a pressure sensor needs to run for a while before it can really stabilize, especially in the first year. The older the pressure sensor is, the more stable it is. In order to minimize the probability of a bad situation and evaluate the pressure sensor better, manufacturers often perform some burn-in tests before leaving the factory.
For the newly produced pressure sensor, the manufacturer will use a heat treatment method for burn-in tests. Therefore, to a large extent, pressure sensors are expected to "move" in the first year. Heat treatment is a form of artificial aging. The pressure sensor is subjected to further testing to determine its characteristics. It includes evaluating the behavior of each pressure sensor at different temperature and the pressure treatment when the equipment exposed to the expected overpressure for a prolonged period of time. These tests are used to describe the characteristics of each pressure sensor. In order to provide a reliable description for the performance of the measuring instrument at different ambient temperatures (temperature compensation), it is necessary. Therefore, long-term stability depends to a large extent on the quality of production. Of course, regular calibrations and adjustments can help correct any deficiencies. However, in most applications it should not be necessary. Pressure sensors that properly produced will work stably for a considerable period of time.
- The importance of long-term stability for the pressure sensor
Nevertheless, it is impossible for pressure sensors to have unlimited long-term stability and accuracy. Factors such as pressure hysteresis and temperature hysteresis cannot be completely eliminated. It can be said that they are characteristics of a pressure sensor. Users can make corresponding plans. For example, for high accuracy applications, the pressure hysteresis and temperature hysteresis should not exceed 0.02% of the total scale. In addition, the physics law have certain limitations on the long-term stability of pressure sensors. Wear and tear testing is required in particularly demanding applications such as wave and high temperature applications. For normal pressure sensors, a continuous high temperature of over 150 ℃ eventually destroys the pressure sensor.
- How to optimize the long-term stability of pressure sensors
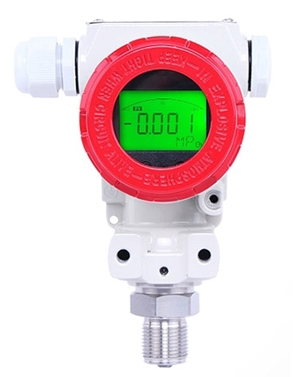
In order to achieve the best long-term stability for the pressure sensor, that is, only a minor displacement occurs during the life of the product. The core component that is the sensor chip must be correct. For a diffused silicon pressure sensor, it uses a diffused silicon core as the core component. Pressure sensors with good stability have already begun to lay the foundation in the production process. Therefore, sufficient silicon chip identification is vital for producing long-term stable pressure sensors. The assembly of the pressure sensor is also decisive. The silicon wafer is glued to the outer casing. Due to factors such as temperature, the material sticking to the chip will move, which affects the mechanical stress on the chip. The result of this is that the measurement results are becoming more and more inaccurate. Practice has shown that a pressure sensor needs to run for a while before it can really stabilize, especially in the first year. The older the pressure sensor is, the more stable it is. In order to minimize the probability of a bad situation and evaluate the pressure sensor better, manufacturers often perform some burn-in tests before leaving the factory.
For the newly produced pressure sensor, the manufacturer will use a heat treatment method for burn-in tests. Therefore, to a large extent, pressure sensors are expected to "move" in the first year. Heat treatment is a form of artificial aging. The pressure sensor is subjected to further testing to determine its characteristics. It includes evaluating the behavior of each pressure sensor at different temperature and the pressure treatment when the equipment exposed to the expected overpressure for a prolonged period of time. These tests are used to describe the characteristics of each pressure sensor. In order to provide a reliable description for the performance of the measuring instrument at different ambient temperatures (temperature compensation), it is necessary. Therefore, long-term stability depends to a large extent on the quality of production. Of course, regular calibrations and adjustments can help correct any deficiencies. However, in most applications it should not be necessary. Pressure sensors that properly produced will work stably for a considerable period of time.